潤滑油
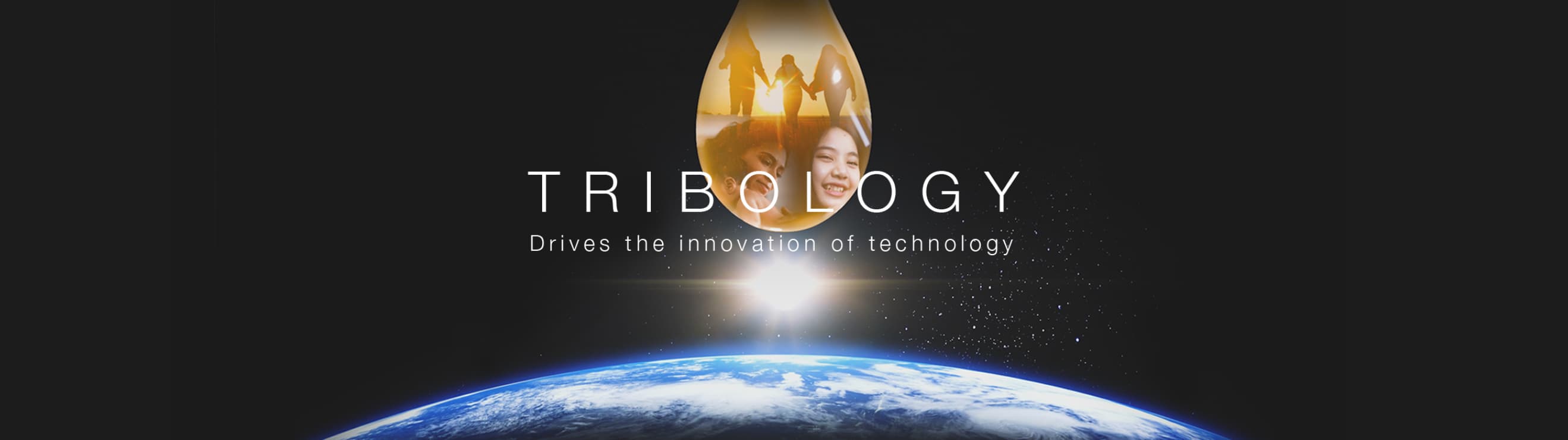
自動車向け潤滑油やグリース、産業機械向け油圧作動油やギヤ油といった工場用潤滑油などを扱っています。世界28カ国に製造・販売・研究開発ネットワークを有しており、お客様の課題やニーズに沿った商品開発を行っています。
基本情報
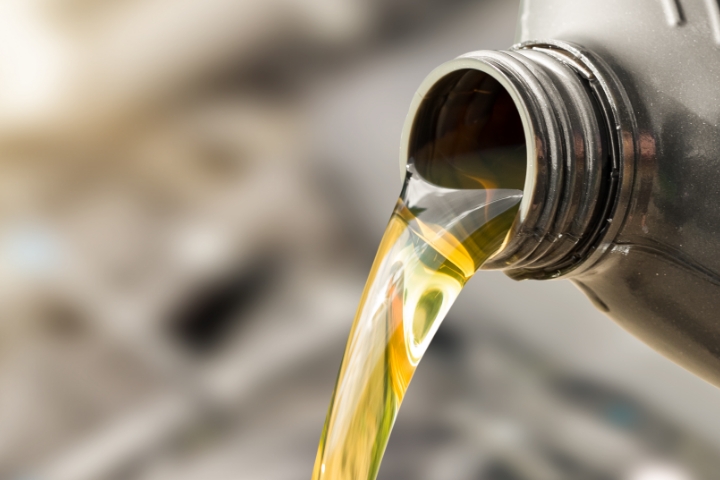
潤滑油とは?
潤滑油とはどのようなものか、身の回りにある潤滑油や、潤滑油と摩擦の関係についてご紹介します。
詳しく知る
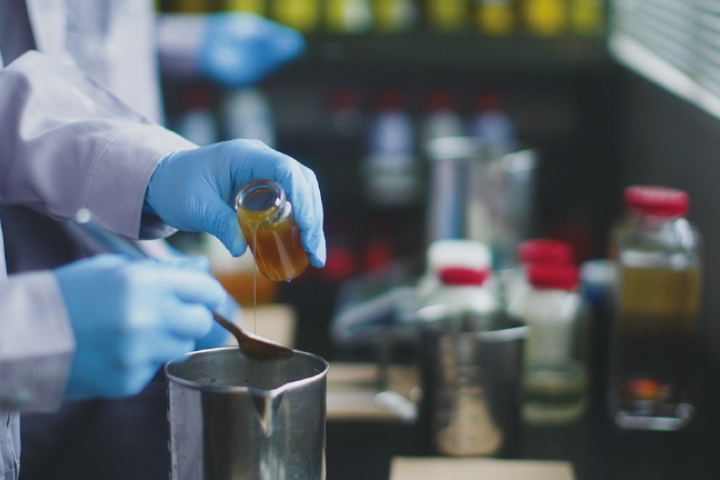
事業の強み
100年以上の歴史を持つ出光興産の潤滑油。世界各国で同一品質の供給体制を確立し、お客様の様々なご要望にお応えします。
詳しく知る
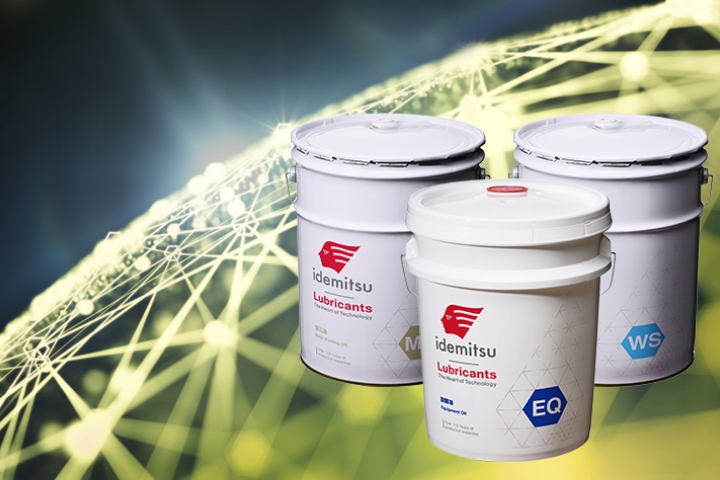
出光テクノロジー商品
お客様の潤滑油に対する課題や問題の解決に貢献する商品開発・技術支援に尽力しています。当社が開発した代表的な商品をご紹介します。
詳しく知る
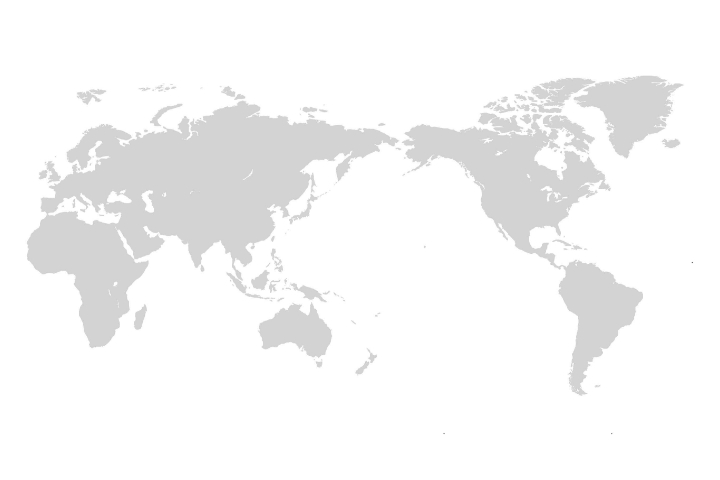
販売拠点
潤滑油の販売を行う国内・海外の拠点をご紹介します。
詳しく知る
製品一覧
適油選定
種類も用途も多様な潤滑油製品の中から、工業用、内燃機用ともにお客様の現場の状況やニーズにあわせた製品をお選びいただくために。当社がお勧めする適油選定表をジャンル別にご覧いただけます。
SDSダウンロード
製品を安全に管理するためのSDS(Safety Data Sheet:製品安全データシート)を提供します。
潤滑油にかける想い The Heart of Technology
当社が培ってきた潤滑油技術はお客様や消費者、そして社会全体のテクノロジーの革新を支えています。当社潤滑油のブランドメッセージ”The Heart of Technology”は、テクノロジーを通じて、真に心豊かな世界を実現したいという私たちの姿勢を表現しています。
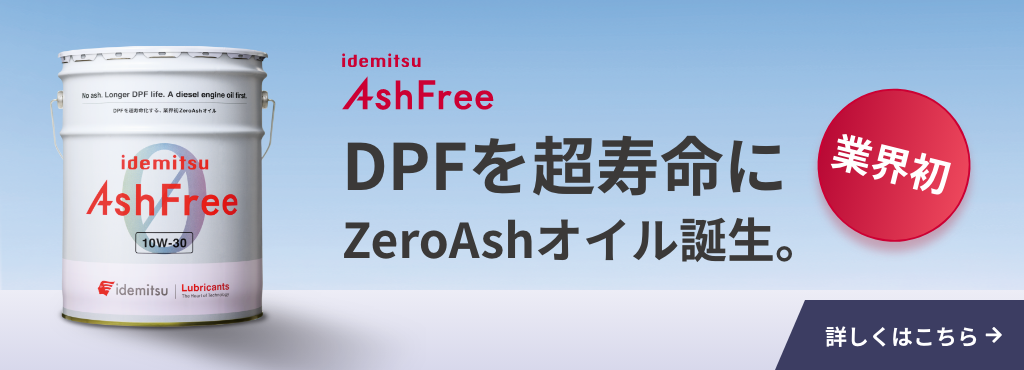