Chiba Complex | Environmental Initiatives
From the start of operations in 1963, we established a green belt around the plant, and it began as a green "park factory" that was considerate of the local landscape and environment.
This was 10 years before the Basic Law on Pollution Control was promulgated, and it became the pioneer of greening and beautification in factories in Japan.
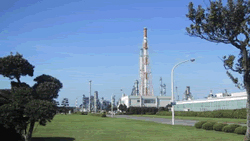
oil district green belt
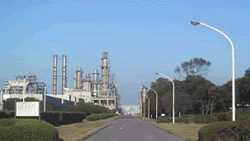
chemical district green belt
Since then, further greening has been promoted, and the Green Belt, Shinji Pond, and Konan Pond now have seasonal flowers blooming and are home to small animals such as pheasants and waterfowl.
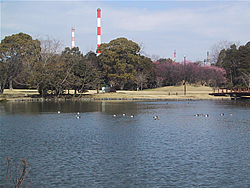
Shinji Pond
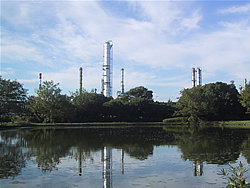
Konan Pond
Environmental policy
We will post the scope of application of our environmental policy and environmental management system.
Chiba Complex
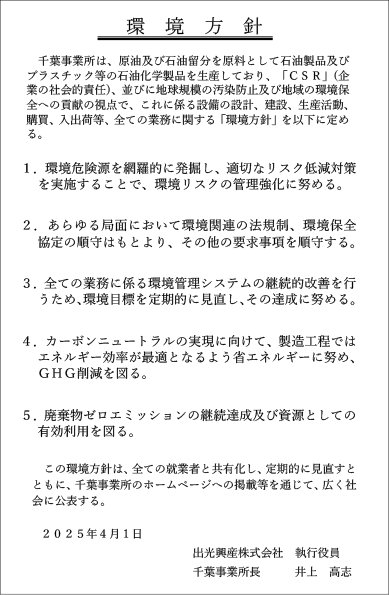
Environmental management system scope
In April 2019, the scope of application that was previously divided between the petroleum site and the chemical site was integrated, and in November 2019, Chiba Complex underwent an extended ISO 14001 audit and was certified.
Chiba Complex
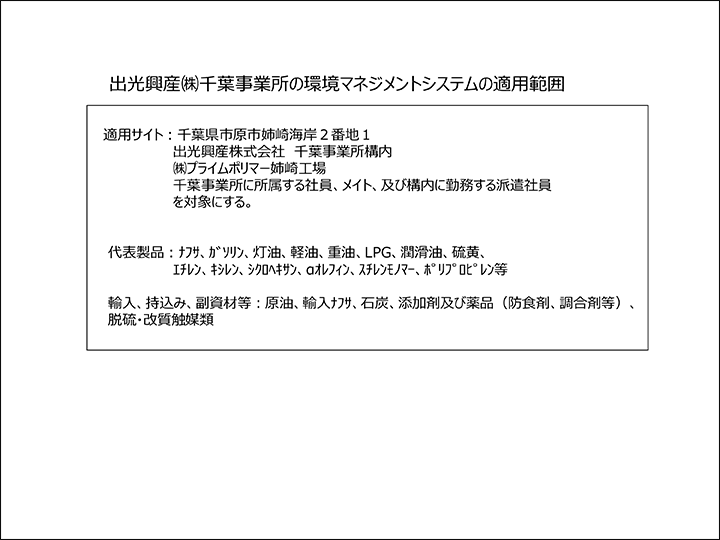
Promotion of energy conservation
The petroleum industry (Petroleum Association of Japan) and the chemical industry (Japan Chemical Industry Association) have each formulated voluntary action plans * that set industry targets for improving energy consumption per unit of production. Chiba Complex is conducting planned energy conservation activities to achieve its energy conservation targets.
*Voluntary action plan:
Petroleum industry (Petroleum Federation): Achieve energy saving measures of 1 million kL of crude oil equivalent in FY2030 through energy saving measures taken from FY2010 onwards.
Chemical industry (Japan Chemical Industry Association): By 2030, reduce CO2 emissions to 6.5 million tons, compared to BAU (Business As Usual) CO2 emissions (converted using 2013 data). The absolute amount will be reduced by 6.79 million tons.
Initiatives to reduce waste
At Chiba Complex, industrial waste generated includes dust collected by dust collectors, sludge, waste oil, sludge (sludge mixed with oil), used catalysts, waste acid, and waste alkali.
In response to this, we are working to reduce the amount of final disposal (landfill) by suppressing waste generation, reducing waste through intermediate processing, and Resources.
Chiba Complex achieved zero emissions ahead of schedule in fiscal 2003 and has continued to do so ever since.
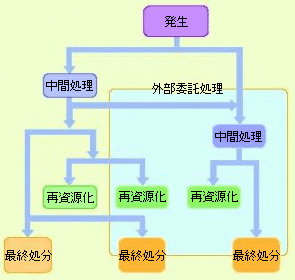
As a concrete initiative to reduce waste, coal ash generated from coal boilers is reused as raw material for cement, housing construction materials, and soil conditioner.
Spent catalysts are recovered as metals and reused as raw materials for cement.
The silicon part of the heat insulating material generated during periodic inspections is used as a raw material for cement or sintered material in the steel manufacturing process, and the urethane part and glass wool are melted and reused as roadbed materials.
*Zero emissions was proposed by the United Nations University in 1994, and is a concept that aims to reduce the amount of waste produced by society as a whole to zero by recycling.
Idemitsu defines zero emissions as the state in which the amount of final disposal is 1% or less of the amount of waste generated.
Environmental measures
Air pollution prevention measures
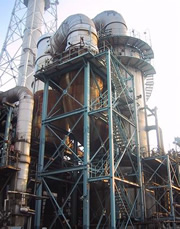
Flue gas desulfurization equipment that reduces SO x
At Chiba Complex, sulfur oxides (SOx), nitrogen oxides (NOx), and soot are generated from boilers and heating furnaces.
Hydrocarbon vapors are also released into the atmosphere from crude oil and product tanks during storage and during shipping.
We are working to reduce SOx by removing it with flue gas desulfurization equipment and turning the low-sulfur gas by-produced from each equipment into our own fuel.
Additionally, hydrogen sulfide generated from heavy oil desulfurization equipment, etc. is treated with sulfur recovery equipment and recovered as sulfur.
NOx is reduced by using low NOx burners, adopting two-stage combustion, and installing flue gas denitrification equipment. Dust is collected using an electric precipitator.
Water pollution prevention measures
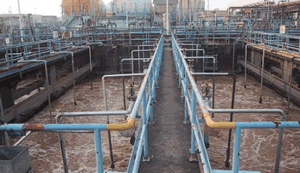
Activated sludge treatment equipment
Regarding the industrial water used at Chiba Complex, we are mindful of water Resources by conserving water and recycling it. Water discharged from the facilities is treated in activated sludge treatment equipment and activated carbon treatment equipment, and hydrogen ion concentration, nitrogen content, phosphorus content, chemical oxygen demand (COD), an index of contamination, etc. are strictly controlled.
Soil pollution prevention measures
The Soil Contamination Countermeasures Act went into effect in February 2003, making it mandatory to conduct a soil contamination investigation when a specified facility that uses hazardous substances is closed down or when the governor deems that there is a risk of health damage.
Based on our mid-term environmental plan, Chiba Complex is conducting a survey to understand the current status of soil contamination and investigate potential risks, including at Complex that are not subject to the Soil Contamination Countermeasures Act or the Environmental Protection Ordinance.
Initiatives to control chemical substance emissions
Of the chemical substances emitted from Chiba Complex,
Substances covered by the PRTR Act
(Act on the Promotion of Ascertaining the Amount of Specified Chemical Substances Released into the Environment and Improving Management of Specified Chemical Substances) include benzene, toluene, and xylene contained in crude oil and naphtha.
Emissions of PRTR substances, which are emitted into the atmosphere as vapor from storage tanks, are reduced by adopting a floating roof system for crude oil and naphtha tanks that emit less vapor, and by collecting vapor with recovery equipment during periodic repairs. I am.
<PRTR substances> FY2020
Unit: t
Ordinance number | Name | emissions to the atmosphere | Discharge into water bodies | Emissions to soil | Moving Complex | Total |
---|---|---|---|---|---|---|
20 | 2-aminoethanol | 0.0 | 0.0 | 0.0 | 33.0 | 33.0 |
53 | Ethylbenzene | 4.7 | 0.0 | 0.0 | 2.5 | 7.2 |
80 | xylene | 1.0 | 0.0 | 0.0 | 0.9 | 1.9 |
240 | Styrene | 13.0 | 0.0 | 0.0 | 1.0 | 14.0 |
296 | 1,2,4-trimethylbenzene | 0.7 | 0.0 | 0.0 | 0.0 | 0.7 |
297 | 1,3,5-trimethylbenzene | 0.2 | 0.0 | 0.0 | 0.0 | 0.2 |
300 | toluene | 6.3 | 0.0 | 0.0 | 0.0 | 6.3 |
349 | Phenol | 0.2 | 0.0 | 0.0 | 2.5 | 2.7 |
389 |
Hexadecyltrimethyl ammonium chloride |
0.0 | 11.0 | 0.0 | 0.0 | 11.0 |
392 | Normal-hexane | 8.0 | 0.0 | 0.0 | 0.0 | 8.0 |
400 | Benzene | 2.6 | 0.0 | 0.0 | 0.0 | 2.6 |
Total PRTR substances | 36.7 | 11.0 | 0.0 | 39.9 | 87.6 |
Items that are handled but have a total release/transfer amount of less than 0.1 t/year are omitted.
The total value may not add up due to rounding.
Gas recovery at lorry station
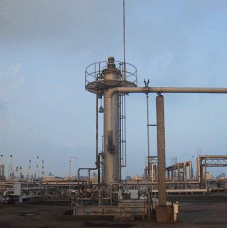
Gas recovery equipment at lorry station
Regarding vapors generated when tank trucks are loaded, volatile organic compounds (VOC) recovery equipment has been installed at truck stations to reduce atmospheric emissions.