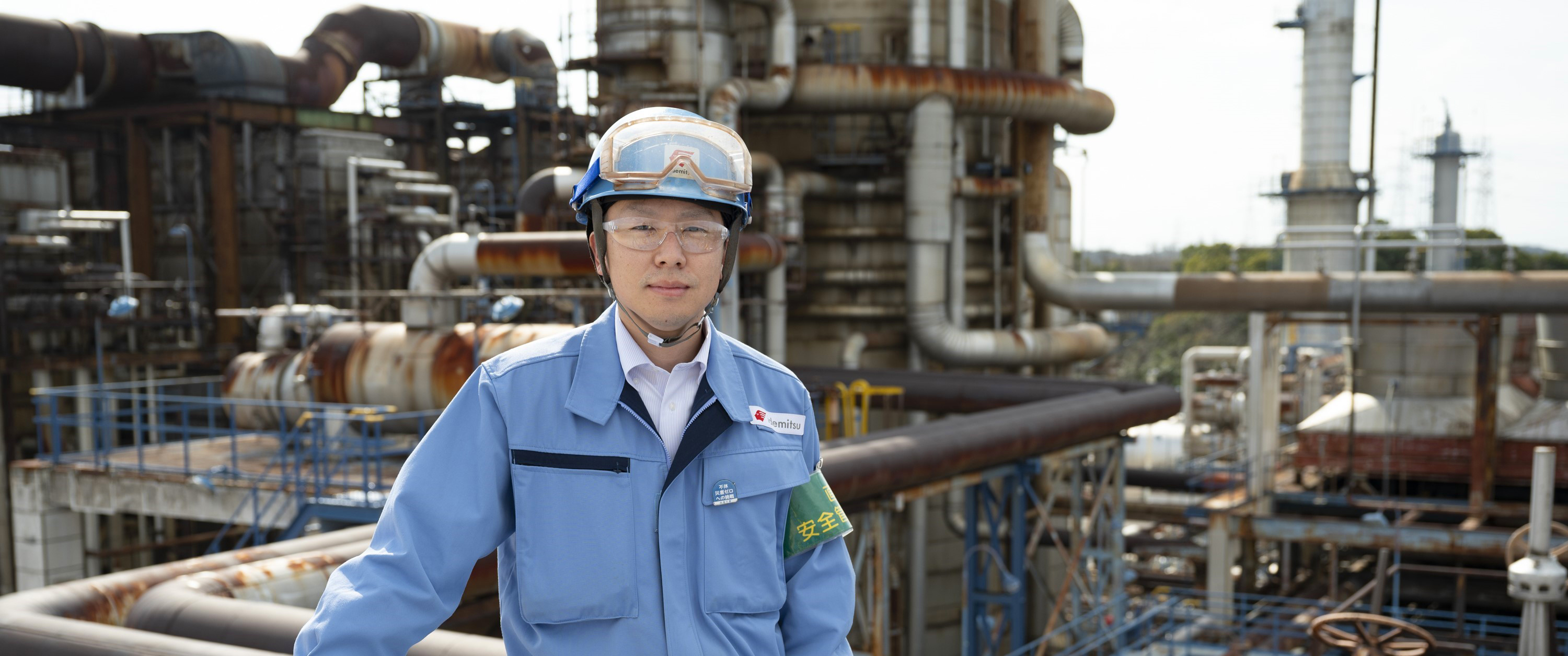
石油製品を毎日
安定供給することで
人々の暮らしを守る。
-
Chiba Complex Refinery Section 1M.YOSHIHARA
Idemitsu Chiba Complex, located in Ichihara City, Chiba Prefecture, is an integrated Complex with Refinery and petrochemical plant, located on a vast site of 3.82 million square meters. Refinery has been supplying petroleum products since its completion in 1963. Refinery operate 24 hours a day without rest, and are required to provide a safe and stable supply of petroleum products. We interviewed a production engineer in charge of the refinery, who supports the lives of people in the Tokyo metropolitan area and continues to make efforts to ensure a constant flow of supplies, on the theme of "protection."
Joined the company in 2007. After being assigned to the Refining Division 1, he worked in shifts operating the equipment for 10 years and in operation planning for 6 years, and will be working in shifts again from 2022. He is in charge of operating multiple equipment, including the atmospheric distillation unit, which is the most upstream unit that processes crude oil. He also works with 8 other members as the shift manager of a 4-shift, 2-shift system (4 teams work 24 hours a day in 2 shifts).
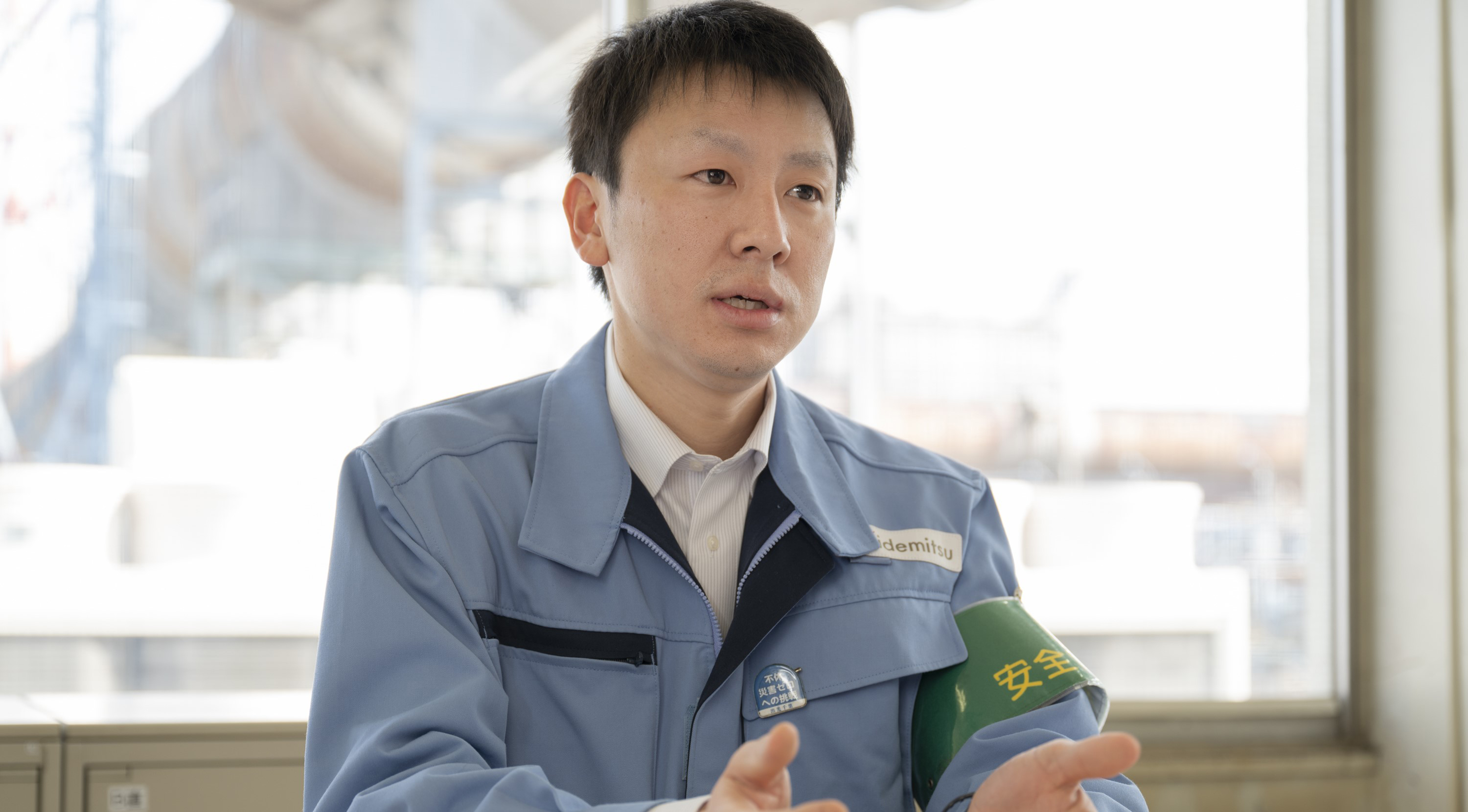
原油から
石油製品を作る
上流装置を
預かるという重責
Refinery equipment runs 24 hours a day.
Chiba Complex has about 50 refining units. It takes one day for Refinery oil to pass through the refining units and become petroleum products. Crude oil is first separated into fractions in an atmospheric distillation unit, a tower about 50 meters high. After secondary processing and quality checks, it becomes petroleum products such as LPG (liquefied petroleum gas), gasoline, jet fuel, kerosene, and lubricants. "In the Refining Section 1, we operate the atmospheric distillation unit, which is at the most upstream stage of the petroleum product manufacturing process, and the equipment at the next processing stage. Our equipment plays a vital role, as downstream equipment may not be able to operate depending on the condition of our equipment. The equipment runs 24 hours a day, approximately 330 days a year, excluding shutdown periods for inspections. It needs to be monitored by human eyes throughout that time."
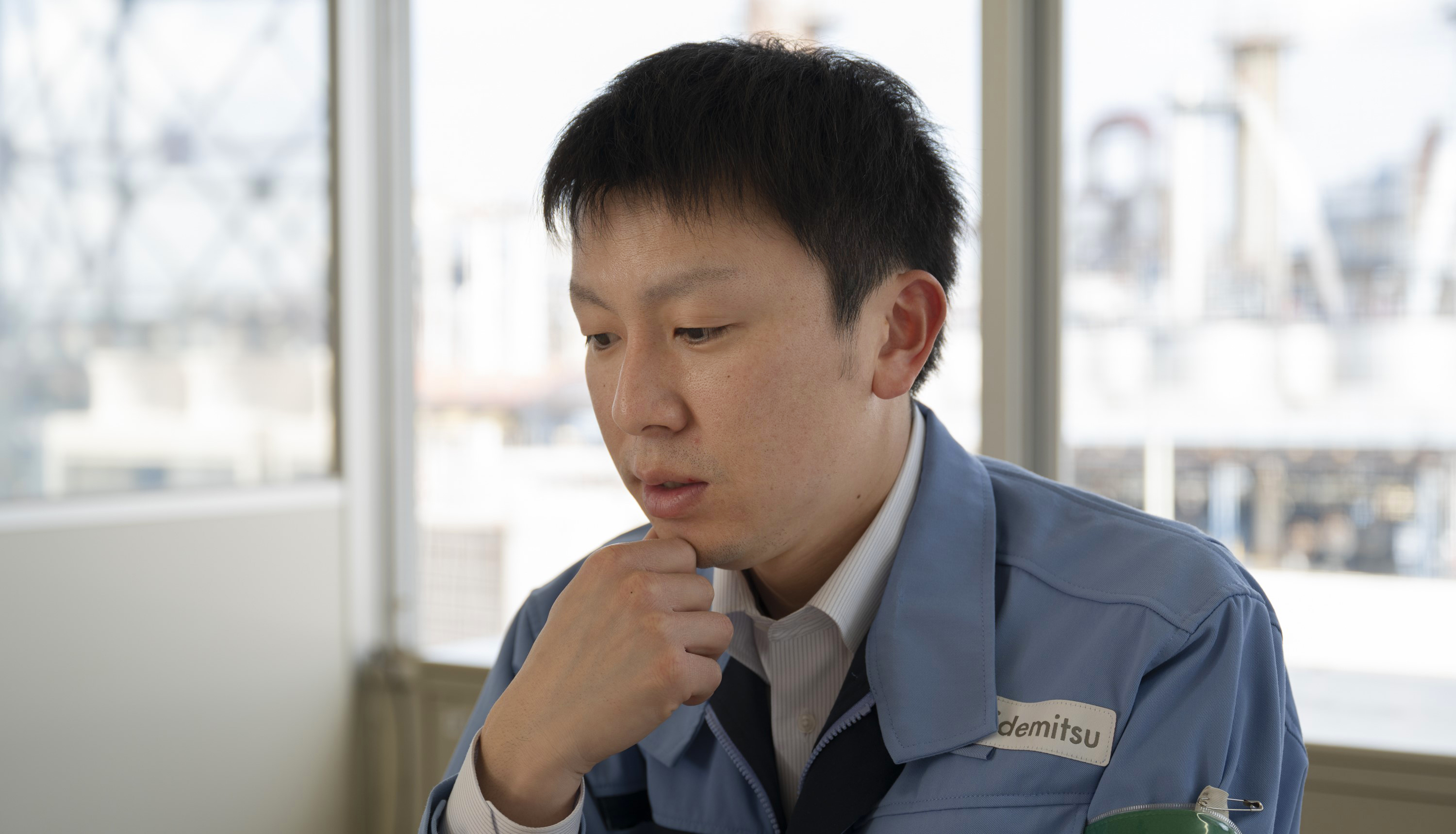
The staff who support the constant Refinery
Yoshihara's day begins at 7:30 a.m. when he takes over from the night shift supervisor, and his work continues until 8:00 p.m. "At the morning meeting, everyone confirms the operations to be performed that day. The equipment is then put into operation. The operator has a 'boardman' who adjusts the flow rate, pressure, etc. on a computer screen in the control room, and We have ”fieldmen” who inspect the equipment, prevent troubles, and make adjustments."Fieldmen handle nearly 10,000 valves of atmospheric distillation equipment alone, as well as rotating machines and inspection items stipulated by various laws and regulations. Apparently it takes 4 to 5 hours to check each and every one of them. "I work 11 hours a day, but I use the time in between to review work, do individual assignments, and do self-study.There are required qualifications for operation, and in our department, we have the qualifications required for hazardous materials handling. I need qualifications as a boiler engineer and a high-pressure gas production safety supervisor.Therefore, I study hard during work hours and after I get home, and then take the qualification exams for each."
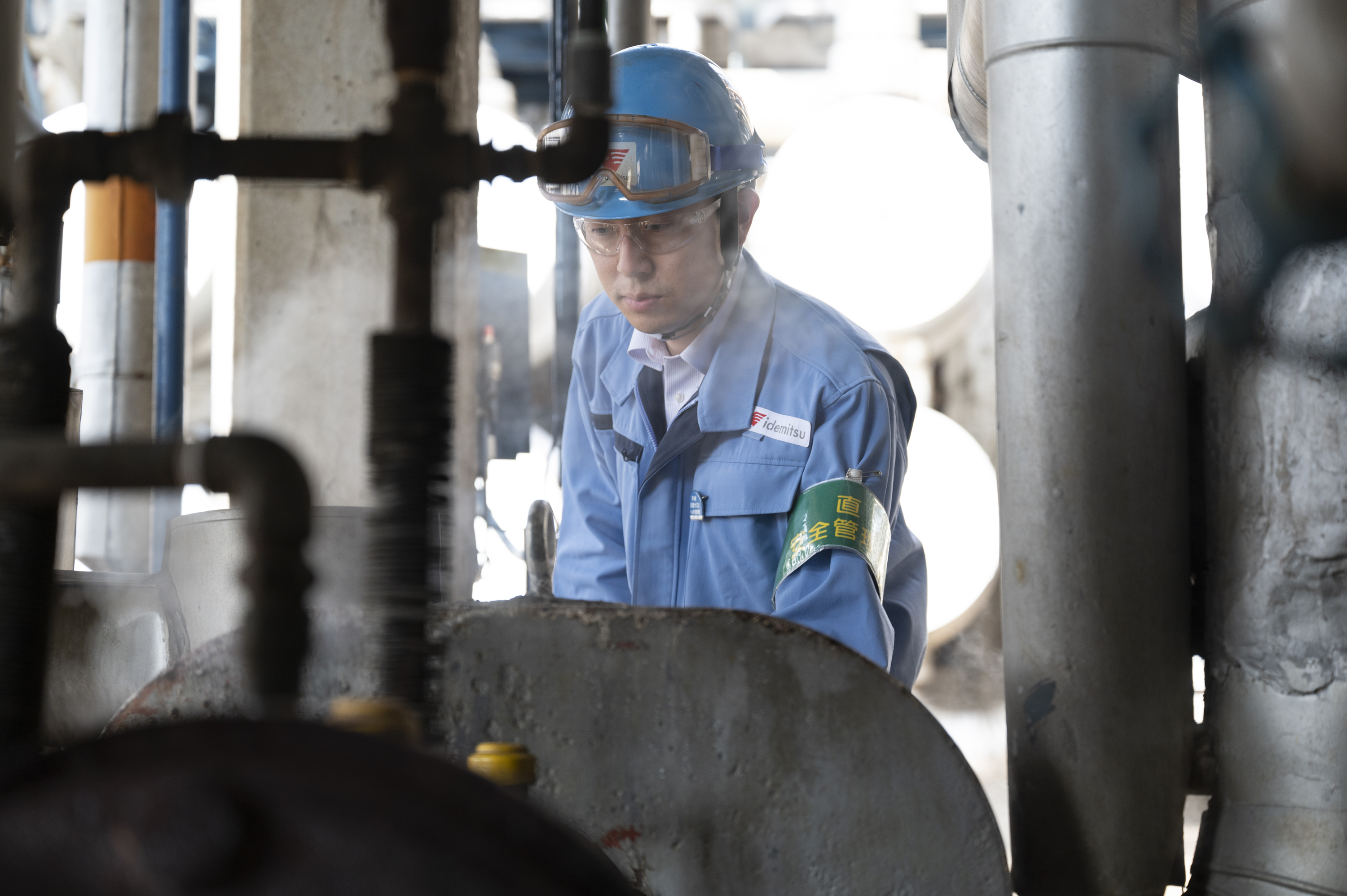
有事の際にも、
安全を確保し
エネルギーの
安定供給を続ける
Handle problems with caution and safety as the top priority
Oil refining involves dealing with machinery, so sometimes unexpected problems can occur. "Our Complex has been in operation for over 50 years, and we experience equipment problems that would never occur in a modern plant. There are many different types of problems. Machines can stop, leak, or not turn on. Water, other utilities, steam, and other things flow through the piping of oil refining equipment. For example, say the cooling water for cooling the rotating machine leaks from a gap in the joint. With household piping, you can just remove it and replace it, but with refining equipment, it's not that easy. To replace the defective part of the cooling water of a rotating machine that runs continuously, you need to carefully consider where to stop it, plan it, and then stop the machine and take action. When an abnormality or change in operation occurs, an alarm goes off, but the alarms are divided into grades, and some parts have two levels of alarms depending on the grade and process. For gradual failures, it is possible to recover after the first level of warning. However, it is possible that a sudden failure can go all the way to the second level, so we train on a daily basis to be able to make instant decisions."
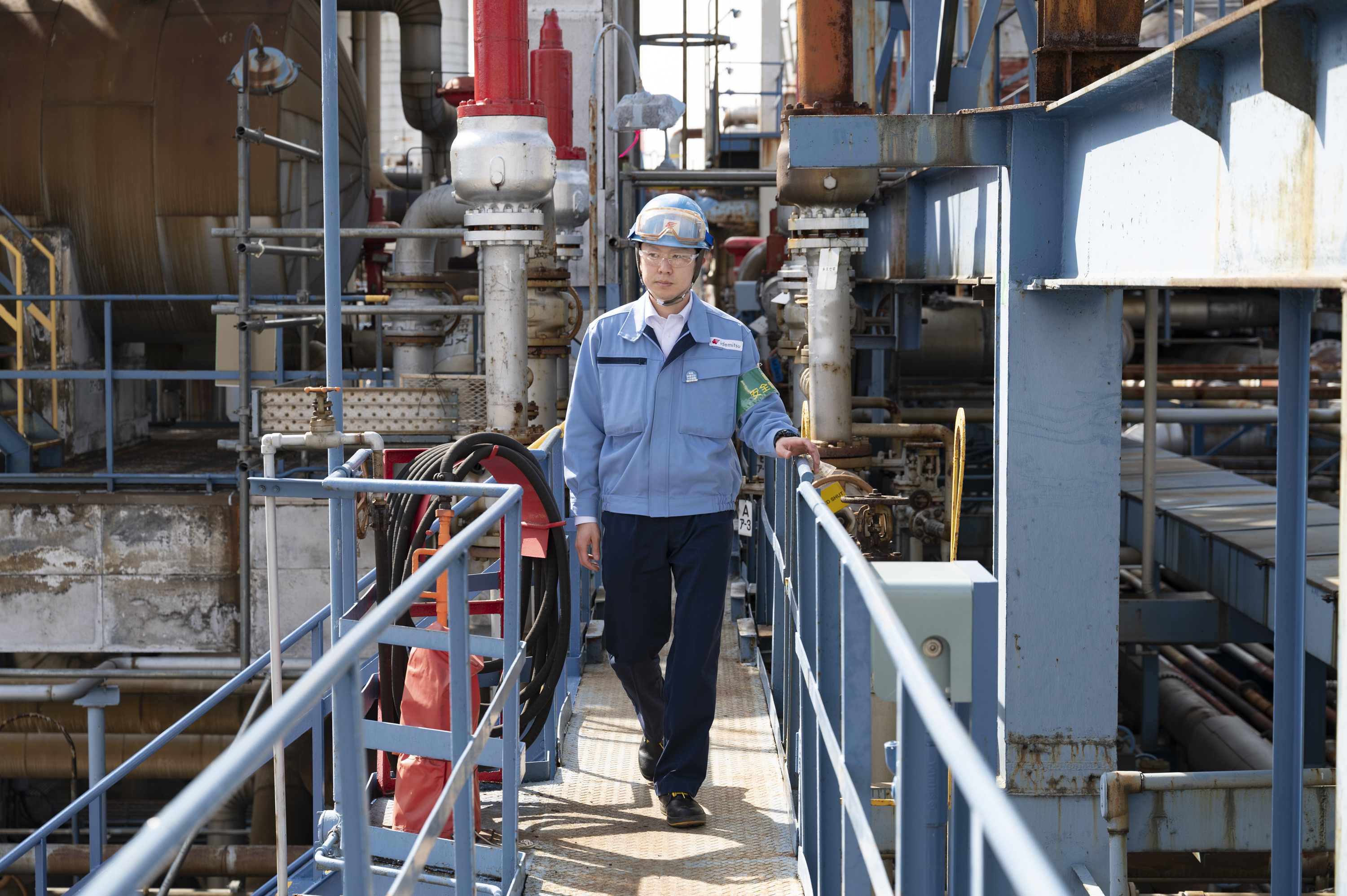
What is required in an emergency is to continue to provide the correct supply.
"During the Great East Japan Earthquake, the news reported huge queues in front of gas stations. I saw it for myself. I remember my boss at the time talking about how important it was to continue to supply infrastructure in the 'right' way. By 'right' I mean a safe and stable supply, and a supply of quality that is within the correct management values. In our case in the Refining Section, this means supplying gasoline base materials and blending them to produce the finished product." What would happen to the equipment in Refinery if a major earthquake were to occur? "In the event of an emergency such as an earthquake, the equipment is designed to automatically stop. We have confidence in the safety of the equipment, but as a worker on-site, I would be under a different kind of pressure, that is, 'We have to start up the equipment again.' If all the equipment stops, we will start it up again after making a detailed plan. We start up each piece of equipment in stages, taking 2-3 to 4 days, so it will take about a month for all the equipment to be operating normally."
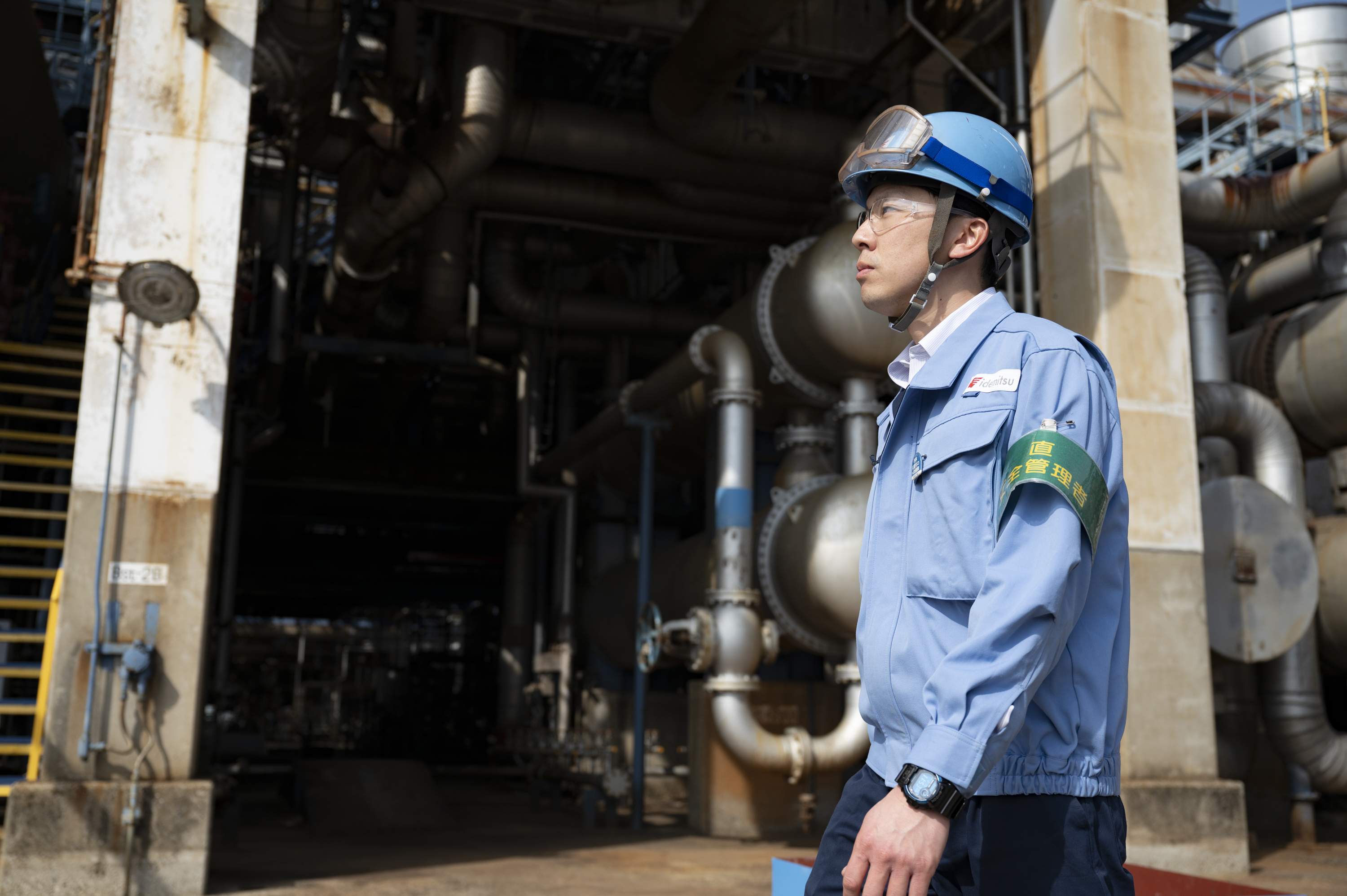
時代が変わっても
人々の暮らしを
守る存在で
あり続けたい
Petroleum products that continue to protect the lives of all people
"Petroleum products are used not only for fuels such as gasoline, but also for plastic products. There may be some household goods that we use every day that actually contain our own products as raw materials. Even if you don't drive a car, most people use electricity every day, and heavy oil and lubricants are needed to turn the turbines of generators. Hydrogen, which is attracting attention as a new energy source toward the realization of carbon neutrality society, can be made from by-product gases produced from petroleum. Since hydrogen is necessary for refining petroleum, we have been handling it at Complex for some time. However, the energy situation has been changing in recent years, and we are receiving requests for hydrogen. As a result, we have had to consider the means of transporting hydrogen and other factors, and consider it as a new business. It seems that the nature of petroleum refining is changing, from simply continuing to produce it to finding ways to utilize what has been used in the past."
To contribute to the energy supply of the next era
"Over the past 10 years or so, there has been a rapid change in the generations, and training of on-site human resources has become an urgent task. When I joined the company, I remember that the majority of the people on-site were in their 50s, but now most are in their 20s. We need to maintain the equipment, but we also need to train people who can understand and use it. From the perspective of a manager, I believe that there is no time to waste, and that we have no choice but to grow together while thinking about how to train people." Even as experienced operators retire from the site, operations continue every day. "Our job is to protect people's lives. In order to protect them, it is important to train people now, and the people we have trained will continue to provide a stable supply for 10 or 20 years. Even if a difficult situation occurs, we want to maintain safety and stable operations."
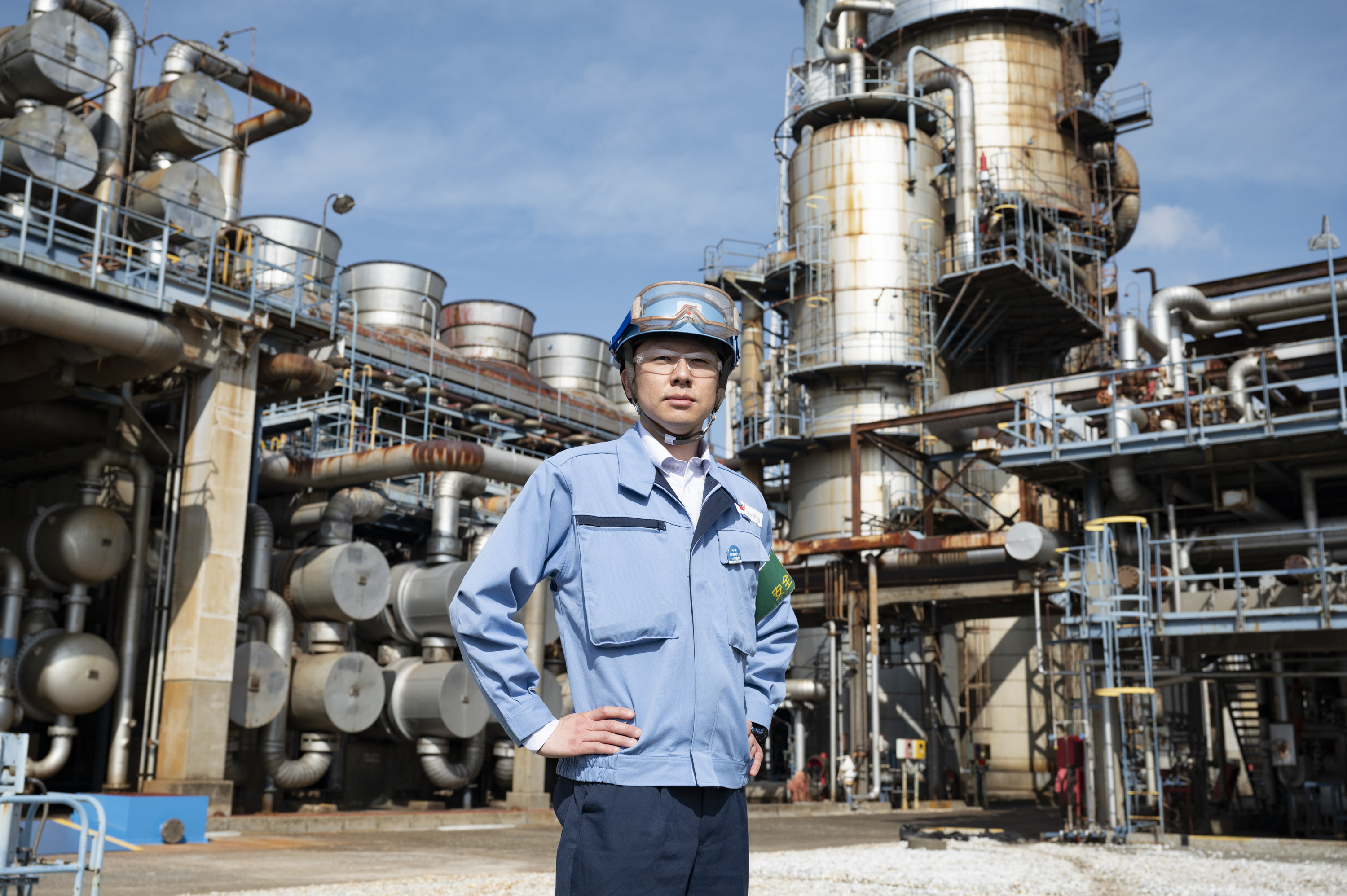
What is a new method of human resource development that transcends the generation gap?
Aiming to develop human resources that lead to safe operations
"Right now, I am faced with the challenge of having to think about a different training method than the education I received.When I first joined the company, when my subordinates were feeling down, my boss would try to cheer them up by drinking. However, in this day and age, things don't always work that way.For example, some people handle things roughly.Even in normal life, things can break when thrown, or unexpected problems can occur. I believe that basic things like treating things with care lead to safety.That's why we need to know how to convey our thoughts and ideas in a way that helps others understand their actions. We are working every day through trial and error to see if things will change.”
*As of March 2024
Related interviews
-
概念を超えた
サービスステーションの
実現によって新しい
時代を切り拓く。2024.03.21 UPPetroleum Marketing Department Gas Station Construction & Development SectionT.USUI -
百年以上もの歴史で
培われてきた
潤滑油の技術と心を
次世代へつなげる。2024.03.21 UPLubricants Department 2 Kanto Lubricants Section 2M.YAMADA -
有機ELの世界に
活路を見出した
先達の意思を継いで
未来を切り拓く。2024.04.30 UPAdvanced Materials Company Electronic Materials DepartmentM. FUNAHASHI