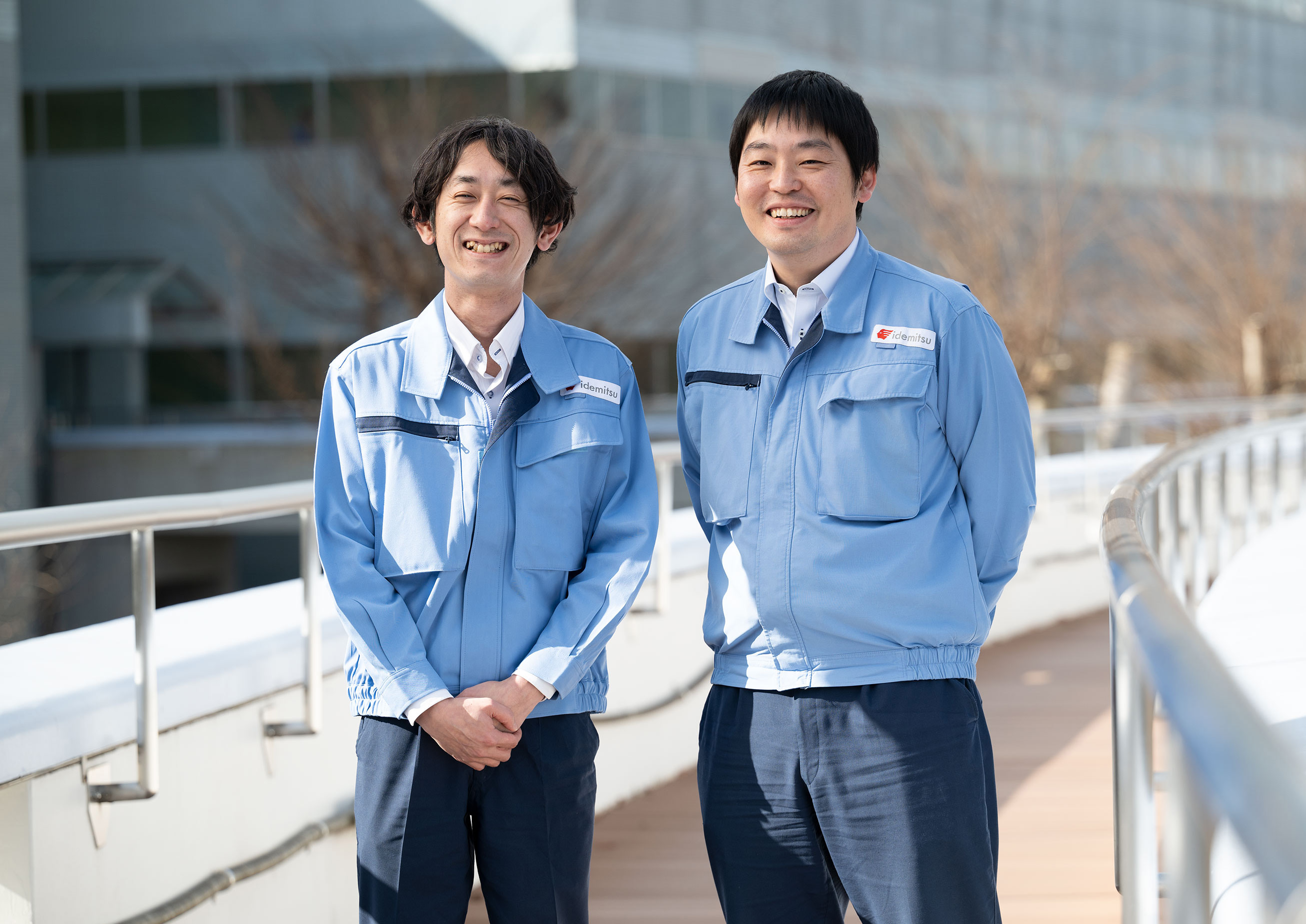
EVにゲームチェンジを起こす
「固体電解質」
社会実装に向けた想いで
前例のない難題を切り拓く
-
Advanced Materials Company Lithium Battery Material Department Battery Material Development CenterN. NAKAYA
-
Advanced Materials Company Lithium Battery Material Department Pilot Plant ProjectY.WASHIDA
In October 2023, Idemitsu Kosan held a joint press conference with Toyota Motor Corporation. There, it was announced that the two companies would begin collaborating to mass-produce all-solid lithium battery, attracting much attention. They will develop and mass-produce "solid electrolytes," a key material for all-solid lithium battery, from "lithium sulfide," which is made from sulfur components generated during the petroleum refining process. We interviewed a member of Lithium Battery Material Department who is involved in the development and mass production of "materials" that do not yet exist in the world, on the theme of "breaking new ground."
N.NAKAYA
Joined the company in 2009 and assigned to Performance Materials Laboratories. After developing manufacturing catalysts for functional resins, transferred to Advanced Technology Research Institute in 2014, in charge of advanced materials development; in charge of materials and process development for solid electrolytes at Lithium Battery Materials Development Center since 2016; team leader in 2018; group leader in 2021; also in charge of Materials Development Center Manager since 2024.
Y.WASHIDA
Joined Chiba Complex in 2006, assigned to Lubricants Section 1. Responsible for the operation of lubricant production plant. Vietnam Business Development Department from 2015 to start up Nghi Son Refinery. After about 5 years of assignment, transferred to Technology & Engineering Center in 2020. Lithium Battery Material Department Engineering Group in 2021, Manufacturing Engineering Group in 2021, and then to Project Management Group in 2024. solid electrolytes He worked as the leader of the commissioning and prototyping operations of the small demonstration test (Plant 1), which is currently undergoing capacity expansion work in preparation for the mass production of the
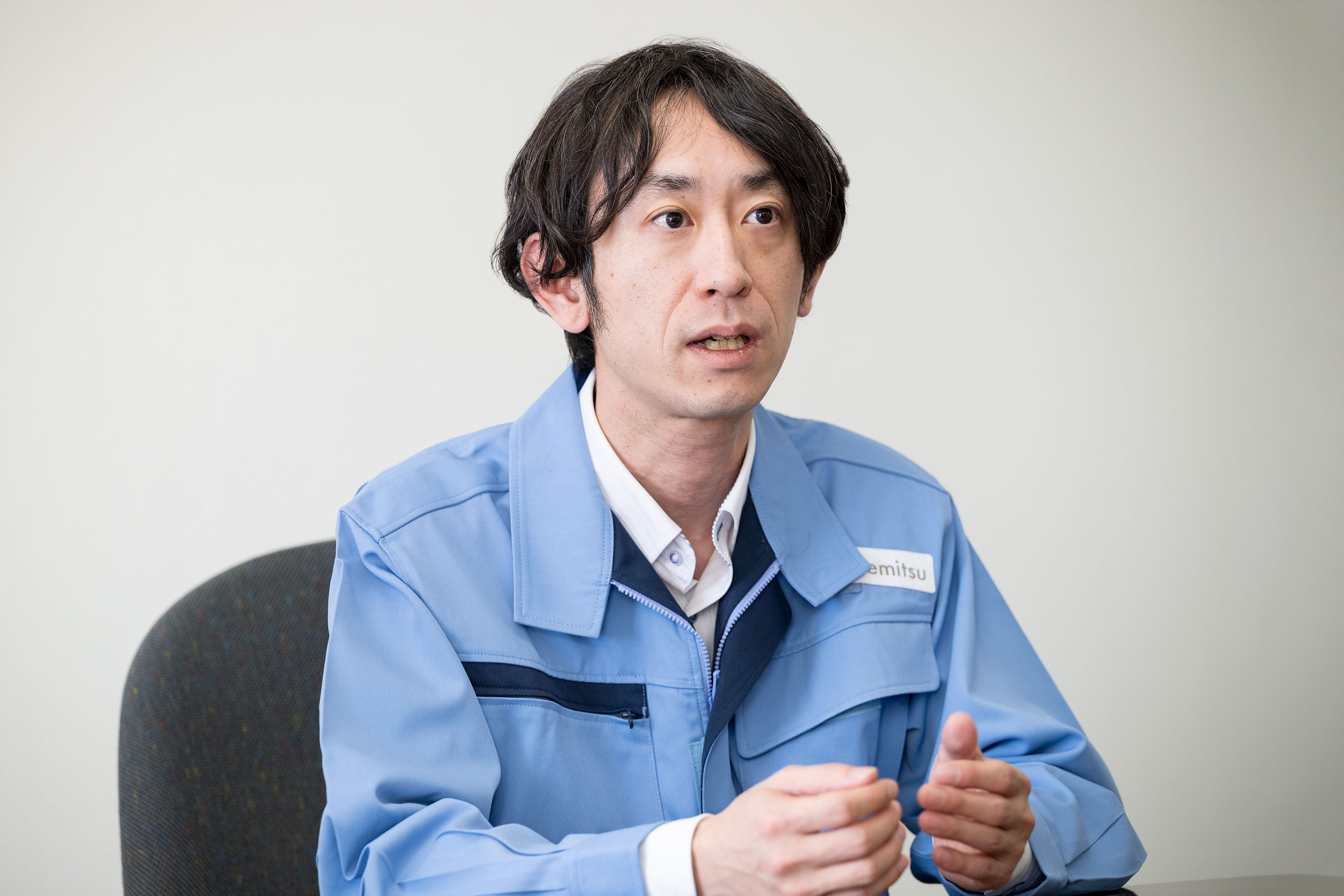
挑戦の始まりは30年前
石油精製の副産物に
付加価値を付ける研究が
今につながる
The turning point was the oil crisis. Instead of relying on oil, the company set its sights on "sulfur components" as it sought new business ventures.
N.NAKAYA "After the oil crisis, activities were carried out at the research institute to create new businesses rather than relying solely on oil. During the oil refining process, sulfur compounds are produced. There was a discussion about whether it would be possible to add value to these compounds and provide them to the world.
Related to this, in the 1990s, it was discovered that using lithium sulfide as a raw material for a resin called polyphenylene sulfide (PPS) makes it easier to produce PPS. As a result, this technology was not adopted for the manufacture of PPS, but it led to the establishment of Idemitsu's own industrial manufacturing technology for high-purity lithium sulfide, so we decided to explore other applications. As we continued our investigation, we came across a certain academic research project, and heard that it was discovered that lithium sulfide could be used as an intermediate raw material for solid electrolytes."
-And that led to the current development of solid electrolytes-
N.NAKAYA "That's right. As we researched, we found that solid electrolytes are an important material that holds the key to the performance of all-solid lithium battery. From there, the target for “lithium sulfide” became “batteries. We had many options: should we become a raw material manufacturer, a materials manufacturer that provides solid electrolytes, or a manufacturer that makes all-solid lithium battery? I heard that among those options, we decided to become a materials manufacturer that could best utilize our mass production technology."
Y.WASHIDA"Regarding lithium sulfide, I heard that they first tested it using a small synthesis facility in a lab, and then built a small bench plant."
-What do you think of your predecessors who have been conducting research and development for 30 years?-
Y.WASHIDA"I think they had foresight, and I'm impressed by how they persevered and didn't give up. I think the seniors had a strong passion for the material, and a determination to get it out to the world."
N.NAKAYA"When we started working on solid electrolytes, the level of awareness was probably just, 'I've heard of all-solid lithium battery in the research field.' But I think my predecessors worked on it with the belief that 'this will provide new value to the world.' I've heard that it was sometimes difficult to get support for working on the development of inorganic materials at a company based on organic chemistry (petroleum). I really respect the fact that they have pushed forward with conviction for 30 years, including difficult times."
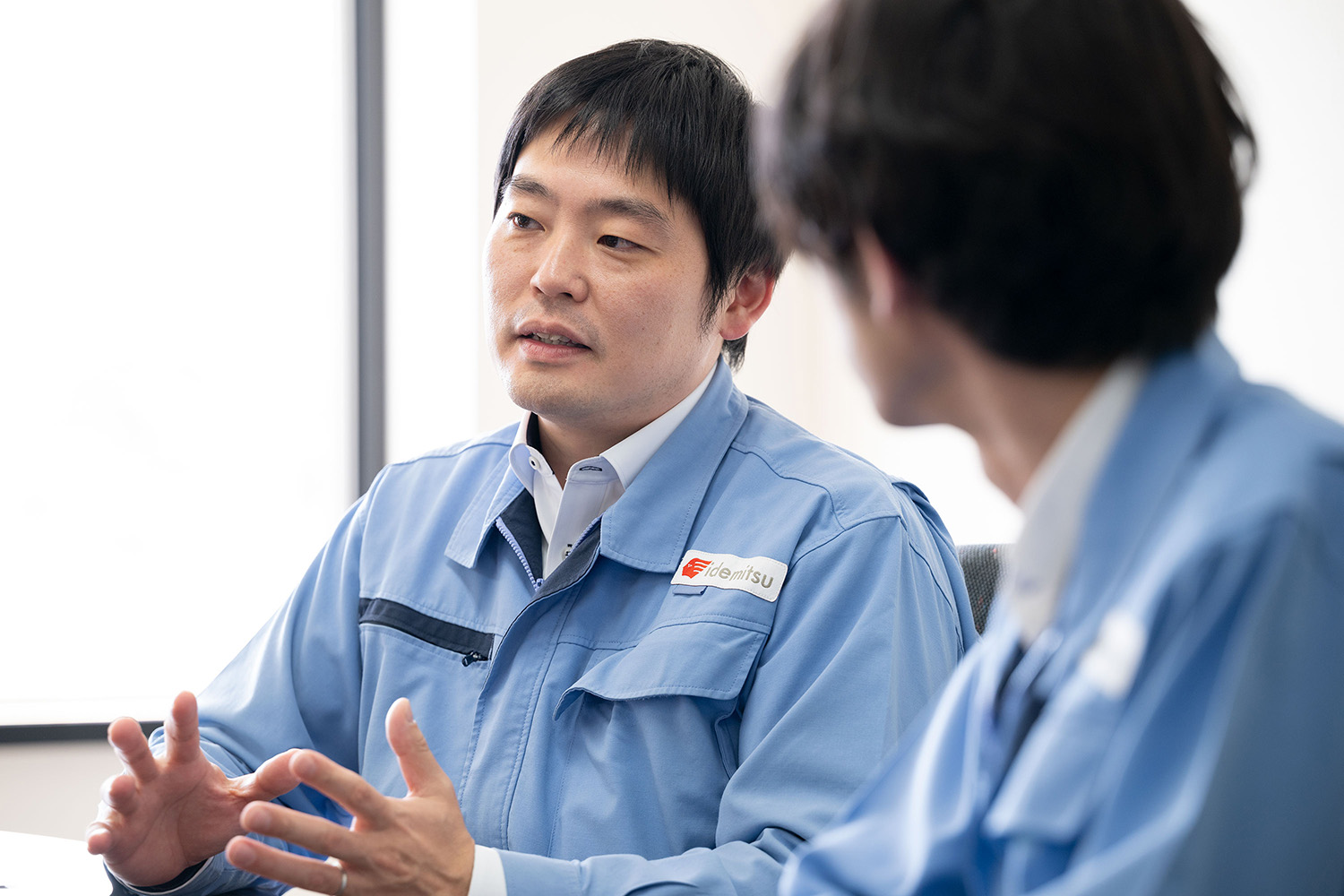
The International Rechargeable Battery Exhibition was a major turning point. The moment a bright light appeared
-Was there a time when you weren't understood?-
N.NAKAYA"all-solid lithium battery used to be called the dream battery. At a time when the performance of liquid lithium-ion batteries was improving rapidly, there was a headwind of 'all-solid lithium battery really be made? Are they worth it?'
One turning point was when we participated in an exhibition in 2009-2010 where we made our own prototype batteries to stimulate the market for all-solid lithium battery. There we highlighted the potential of all-solid lithium battery, such as their heat resistance and safety. As a result, I heard that we started receiving contact from automobile and related manufacturers."
Y.WASHIDA"I believe Idemitsu was able to contribute to creating an opportunity to discover the possibilities and feasibility of all-solid lithium battery."
N.NAKAYA "I heard that it was encouraging to hear from an automobile manufacturer. In fact, that was the catalyst that led to a full-scale collaboration with Toyota, so I think that was the biggest turning point."
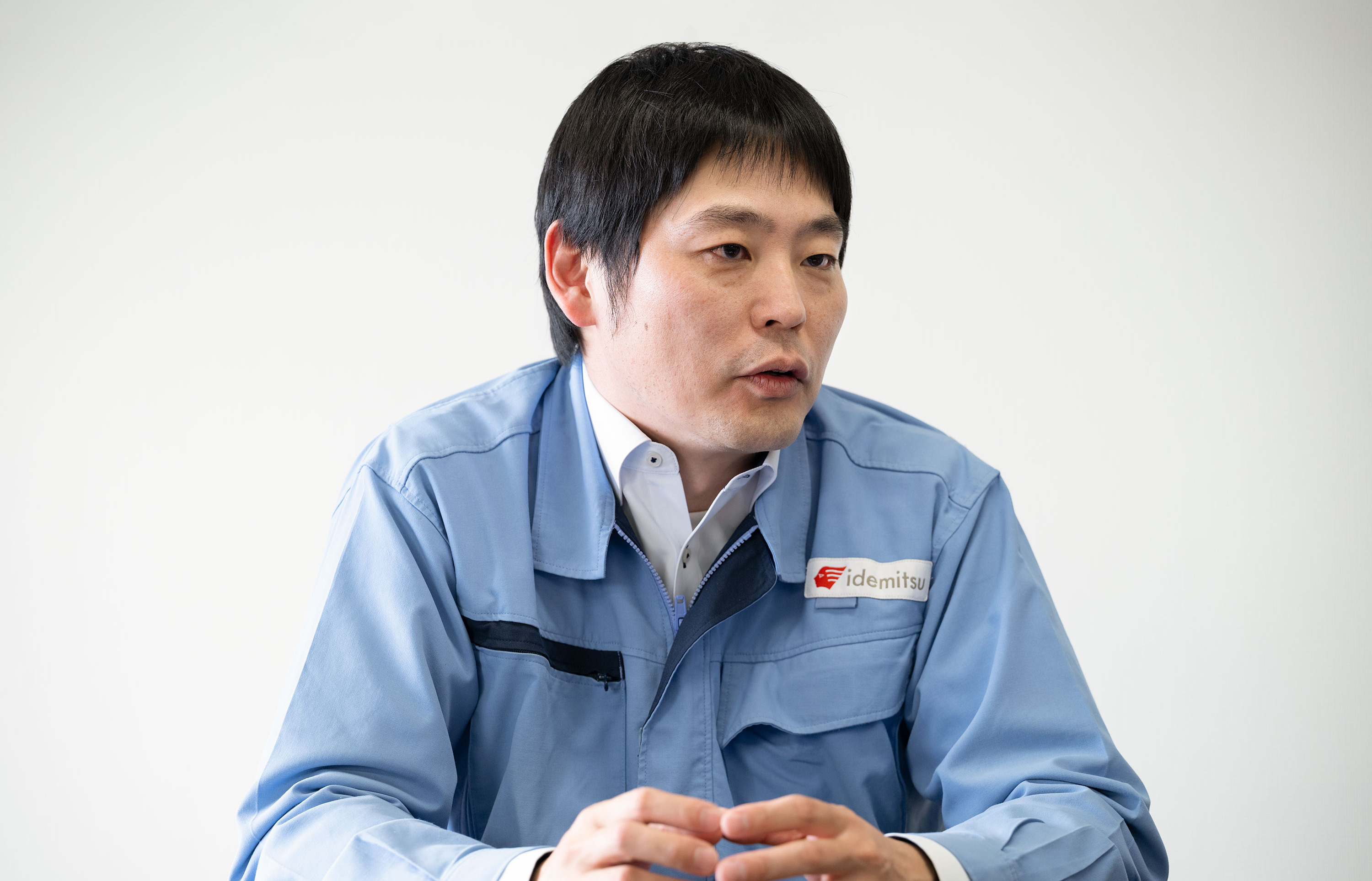
世にないものを
この手で作り出す
トライ&エラーを繰り返して
着実に前に進む
"I have no choice but to do it. I'll take responsibility for it. I leave it to you."
In 2019, Idemitsu Kosan's Advanced Technology Research Laboratories was hit by the storm caused by super typhoon No. 19 and suffered severe damage. At that time, the work of the "solid electrolytes" development team was reaching a climax.
N.NAKAYA"A major typhoon hit us at a time when our customers were about to select materials and we needed to rapidly improve our materials.... The research area was completely cut off from power and water, and we were ordered not to come to work. Normally, research would have come to a halt, but we decided to 'make up our minds and do everything we can.'
Fortunately, the nearby Chiba Complex did not experience any power or water outages. So we removed the experimental equipment from the laboratory ourselves, loaded it into a car, and set it up at Chiba Complex, creating an environment where we could conduct experiments. Although it is rare for laboratories to have shifts (taking turns), not only researchers but also production technology staff came together to set up a shift system and work on improving the materials, somehow overcoming the difficulties."
-Was the deadline for the report imminent?-
N.NAKAYA"Yes. We were in a critical situation, because if we continued to wait for the system to be restored, we might not be able to meet the deadline for providing the next improved material. Normally, we would make several improvements before selecting a material, but of course the other party had their own development plans and deadlines, so there was a limited window of opportunity to receive feedback on the material we submitted. I was desperate, as I wanted to seize these opportunities and bring our technology closer to the target. At the time, when I was about to give up, my boss told me, 'I'll take responsibility. You're the only one who can do it, so do it.'"
Y.WASHIDA"That's a nice thing to say."
N.NAKAYA"Because I was in a leadership position, I wanted to continue my research even under those circumstances. However, I was very worried about whether the members would follow me...My boss told me clearly, 'Don't worry about that. Only you can do it, so please lead the members.' That made me feel at ease."
Y.WASHIDA"I feel like there are a lot of bosses at Idemitsu who would say that."
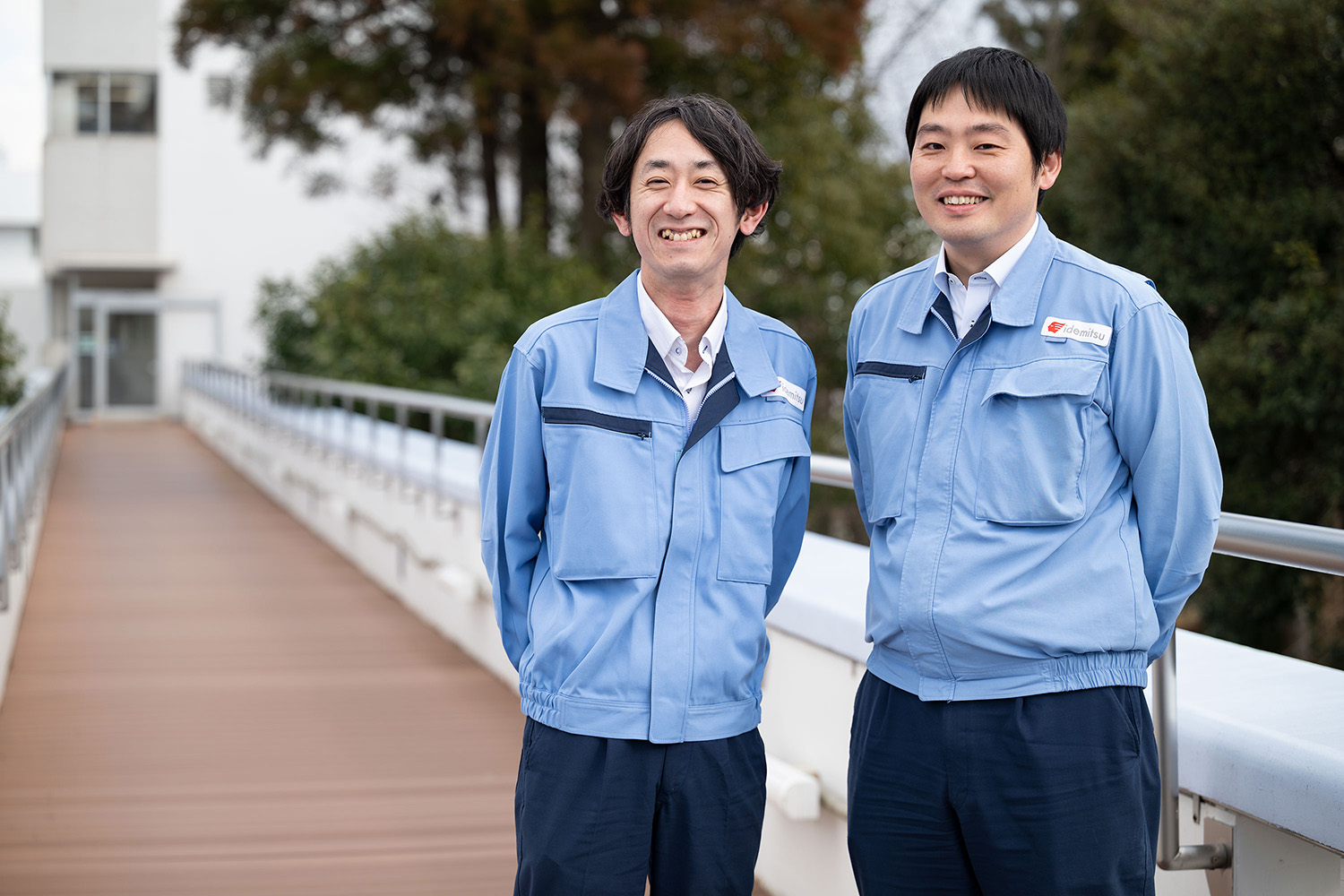
Powder processing is difficult even with advanced calculations and simulations
In the automotive industry, with the spread of BEVs, issues such as long charging times and short driving ranges have become apparent with liquid lithium-ion batteries. Hopes are high for the practical application of all-solid lithium battery, which are expected to improve these issues and become a game changer in the market.
N.NAKAYA "Normally, material manufacturers are given target values by their customers and work to achieve them. However, there are no set target values for solid electrolytes. We make hypotheses, test them, and if they don't work, we think together with the customer about what to do. Building the technology together while working together is the most difficult part of development, but it's also engagement. Because we are creating something that does not yet exist in the world, all of the challenges we face are 'world-first challenges' and no one has the solutions. We have to overcome them ourselves.
Also, solid electrolytes are very fine powders, which can be difficult to handle. For example, if you pass a liquid through a bent straw, it will flow smoothly from top to bottom, but if you pack the powder into the straw, it won't fall out, right?"
Y.WASHIDA"It gets caught on the curved part."
N.NAKAYA"The same thing happens in the mass production process. The development and technical challenges lie in how to make the powder flow smoothly for mass production."
Y.WASHIDA"We conduct various simulation experiments, perform flow analysis, and have other departments calculate the movement of powder in 3D. We proceed with the design after verifying the theory behind how the flow will be when scaled up in a certain way.
Because it is a powder, the yield is likely to decrease and adhesion will increase. We will verify in a small demonstration facility where to install a knocker (a device that uses air power to knock on pipes, etc.) to shake off the accumulated powder, and then scale up the system."
N.NAKAYA "We have them analyze where the adhesion originates, and then we reflect that information in the facility design. That's a very advanced approach."
Y.WASHIDA"But it's just a calculation. We won't know until we actually try it."
N.NAKAYA"That's one of the difficulties of development. You don't know how to scale up powders until you try it. There are many things you can't understand just by chemical engineering calculations or simulations."
Y.WASHIDA "Even with a supercomputer, no one can calculate what actually happens at a microscopic level. So I think it will be difficult to scale up significantly unless we take small steps at a time."
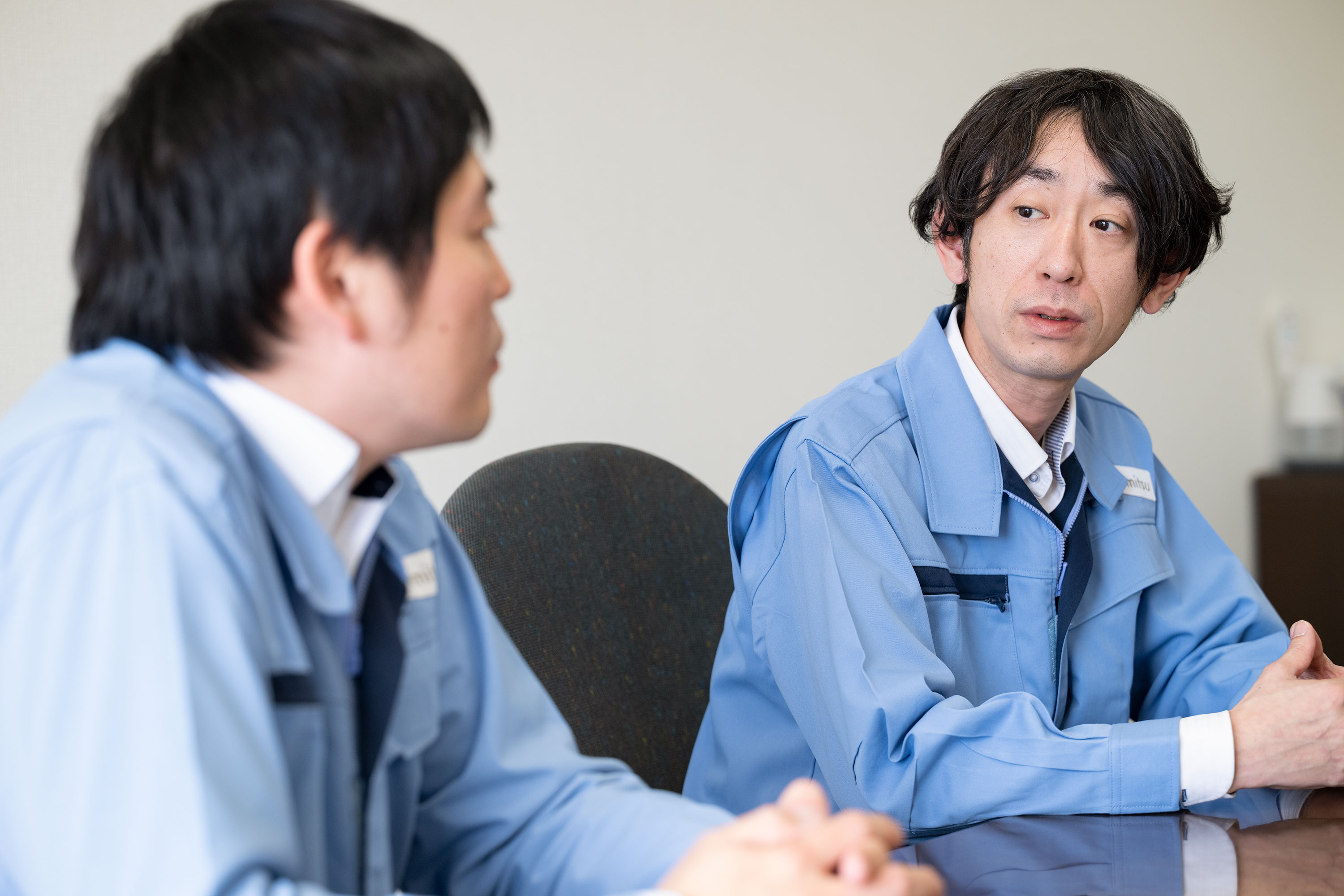
社会実装に向け
開発と並行して
量産を進めるために
日々問われる判断
Immediate decisions are required based on what happens on the day
In October 2024, Idemitsu Kosan will begin basic design work on a large-scale pilot device for "solid electrolytes," a material used in all-solid lithium battery.
Y.WASHIDA "The baton was passed to us after we had reached a milestone - the decision on the basic design of the large-scale pilot facility. I am currently involved in expanding the capacity of the small-scale demonstration facility, and this expansion is intended to verify mass production technology with the large-scale pilot facility in mind. As construction of the new equipment progresses steadily, I have been working behind the scenes to establish the mechanisms and logistics necessary for operation. Once these two are combined, we will finally be able to carry out actual trial operations. Our mission is to complete the expansion of capacity as planned and proceed with the verification of mass production technology, so we need to respond quickly to any issues that arise on the day and at the site. When we start up new equipment, something happens every day, but we quickly take the next step and set priorities as we move forward."
The difficulties of mass-producing powder that far exceed imagination
Y.WASHIDA "I'll explain mass production using the Imoni Festival in Yamagata as an example. At the Imoni Festival, a pot with a diameter of 5 to 6 meters is set on a large stove, and several excavators are used to stir the ingredients together to make the product."
N.NAKAYA "How to make Imoni (lol)"
Y.WASHIDA"At home, you cut the ingredients, put them in the pot, and mix with a spatula... but mass production requires a completely different size and thickness of pot. A household pot is only a few millimeters thick, but a mass-produced pot is only a few centimeters thick. If you apply heat from the outside, only the surface will heat up. If you don't mix evenly and do various other things, this part will be hot, but this part will always be cold. You may be able to calculate how heat is transferred, but when microscopic worlds overlap continuously, you don't know what will happen. That's the difficulty of mass production."
N.NAKAYA "And the difficult part is that it's a powder. Heating a liquid is completely different from heating a powder."
Y.WASHIDA"I really think so. Liquids flow. If you heat them up, convection will occur naturally."
N.NAKAYA "If you keep heating water in a kettle until it boils, it will always reach 100 degrees no matter where you measure it. But if you put flour in a pot and put it on the stove, the surface that's touching the pot may be over 100 degrees, but the inside isn't warm."
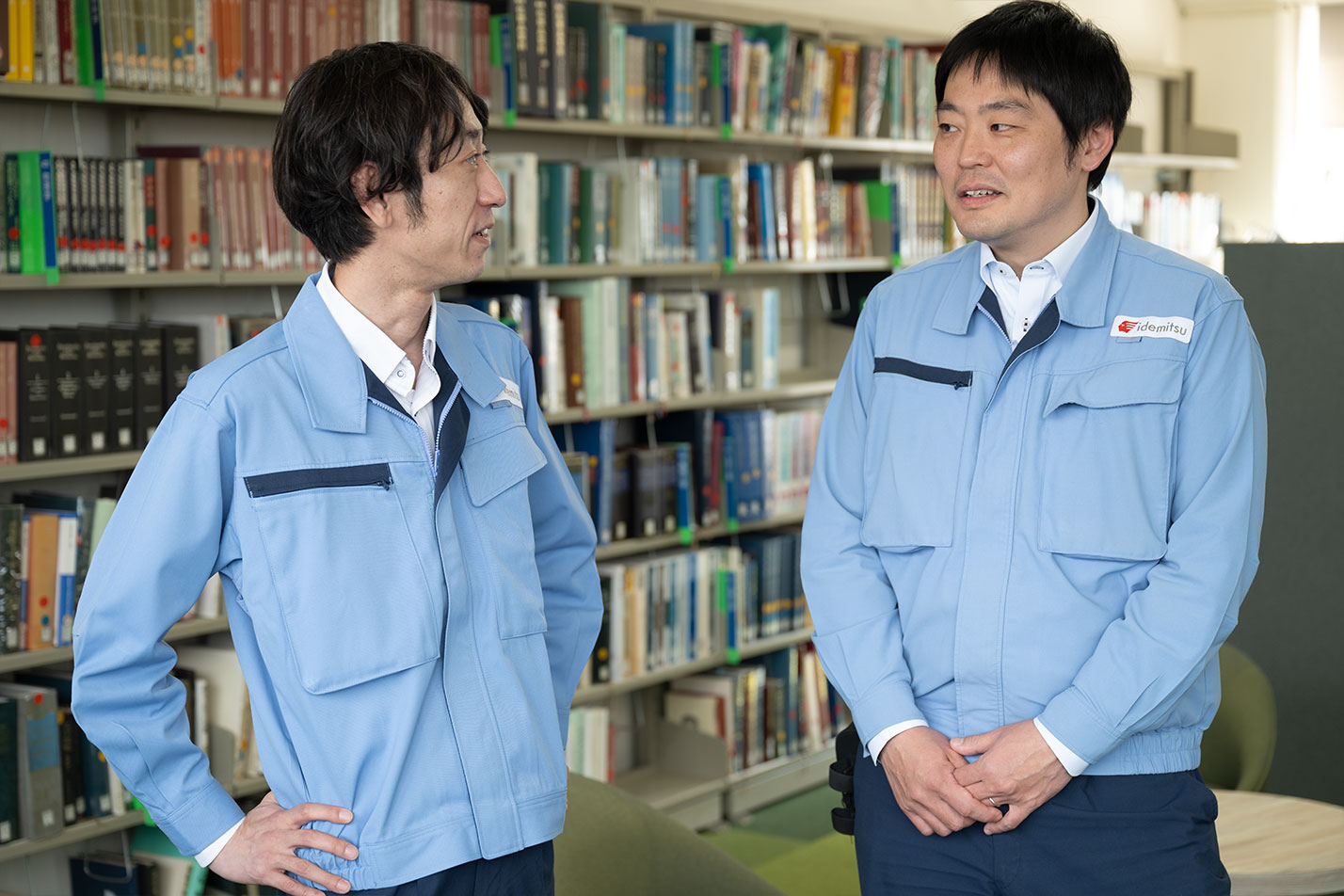
Someone has to make the final decision. That's why we need to discuss it.
-Generally, the design of the mass production plant begins after the material specifications and mass production method have been decided. This time, you said that you are working on both in parallel, but what are the difficulties?-
Y.WASHIDA "There is still room to explore the best process. People involved in equipment construction projects plan their processes with the goal of 'completing the equipment by this date.' Specifically, they evaluate profitability, draw up a basic plan for the equipment, proceed with the design, procure materials, construct, and test run it. However, as we proceed with mass production verification of 'solid electrolytes,' we sometimes find that a different process can produce more, or that it can be made more simply.
In such cases, it is necessary for the materials development side and the plant design side to negotiate and proceed with the study. If someone does not make the final decision, the product will not be able to be provided to the customer. The project leader is required to make some tough decisions."
-If the verification results are not satisfactory, do you ever consult with the material development team about changing the powder design?-
Y.WASHIDA"When things get difficult, we all get together and talk about it. However, the target performance of the material is more or less set, so we consider ways to change the operation or process as much as possible to match that."
N.NAKAYA "Tough people like Washida-san say, 'We have no choice but to do it to make it happen,' but we also sometimes consider whether there is any room for tweaking the material specifications, taking into account the technical difficulties of the manufacturing process."
Y.WASHIDA "Lithium Battery Material Department is compact, and there are many opportunities to talk, so decisions can be made very quickly. However, whereas a large organization would distribute the workload, a small organization can mean a higher workload per person. In a small organization, everyone needs to be an expert to a certain extent in order for things to function, so I think that's one of the difficulties."
N.NAKAYA"Unlike an established business, the things that need to be done change daily, so of course the scope of what you do also changes. When work gets dropped and the question arises of 'who will pick it up?' some people may take it as 'I didn't think it was my job, but now I have to pick it up.' Because things are changing so rapidly, sometimes some members can't keep up emotionally, but I feel that Washida-san provides solid support."
Learning how to blend in with colleagues during my time at the Nghi Nghi Son Refinery in Vietnam
Y.WASHIDA"How you speak and creating a good atmosphere are very important in an organization. It's okay to get angry, but I try to remember to switch gears and speak normally afterwards. If I remain angry for too long, everyone will get fed up, so I try to end it as quickly as possible."
-Was there any particular reason that triggered this?-
Y.WASHIDA"I have been involved in the launch of Nghi Son Refinery since 2015. I worked like a horse, dealing with changes in the plan and problems. I think I was able to overcome all of this because I was determined to launch Nghi Son Refinery.
At the time, I was young and sometimes spoke harshly to my Vietnamese colleagues or gave instructions without fully respecting their culture and way of thinking. Many Japanese had returned to their home countries, leaving only a small number of Japanese people, and I was tasked with taking on a major project. Most of Manager and the head of the operations department were foreigners, and I was just one of the staff. What I learned then was that it is important to convey your feelings, but you have to speak with respect for the other person. If you don't do that, people will never take action."
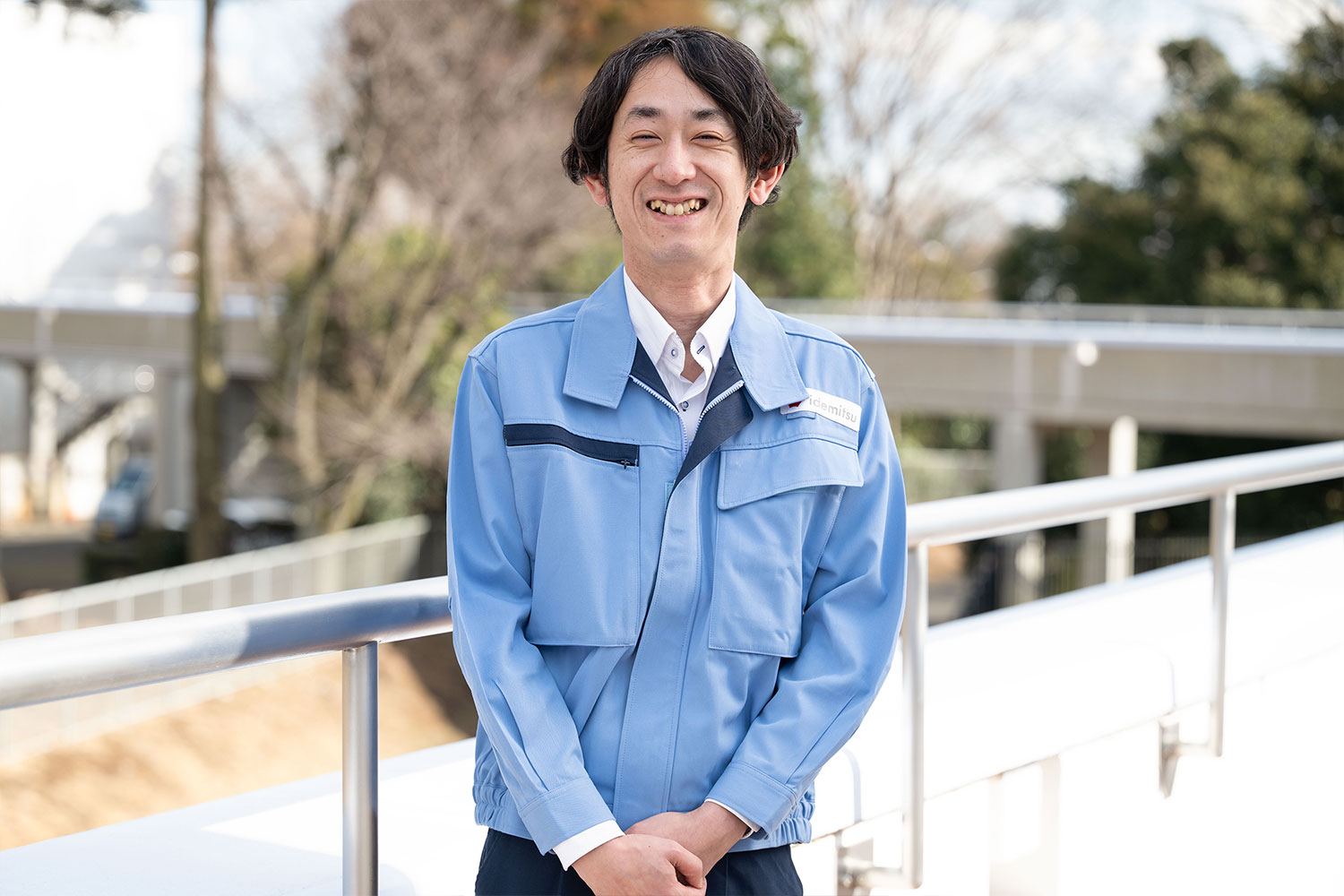
How did you feel when you decided to work on lithium battery materials?
-We have heard about the difficulties of developing and mass-producing something that does not exist in the world. What were your honest thoughts when you first became involved with lithium battery materials?-
Y.WASHIDA "I was grateful to have the opportunity to try new things. I joined the company as a production engineer, and when I was transferred to Technology & Engineering Center I became a staff engineer. I went from operating the equipment to making it. From the beginning I had the goal of trying new things and building my own equipment."
N.NAKAYA "When I joined this project, it was in the middle of rapid growth, so I was honored to be invited. It was a different field from what I had been involved in up until then, but I was happy to be invited to work in a field that will carry the future of Idemitsu."
In February 2025, Idemitsu Kosan announced its decision to build a lithium sulfide manufacturing facility, taking another step towards provide for society.
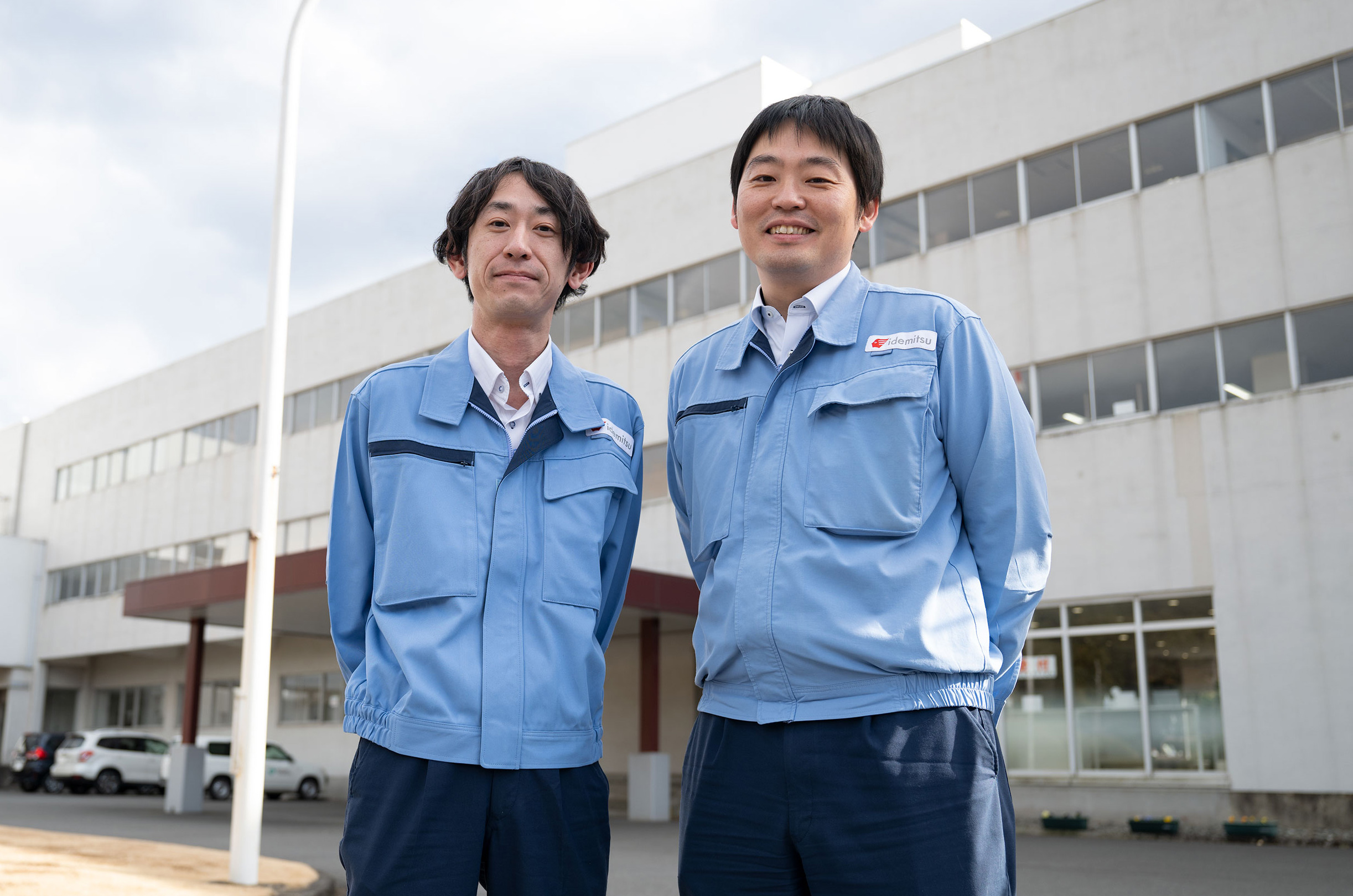
技術のバトンを受け継ぎ
夢と呼ばれた未来が今、
現実になろうとしている
その想いと覚悟は
What is the biggest hurdle that must be overcome in provide for society?
N.NAKAYA"No matter how good a product you can make on a lab scale, it's meaningless if it doesn't perform as well when mass-produced. Mass production is the biggest hurdle. And it's important that the product performs well when it's on the customer's side and that it can be used as a material. Our mission and challenge is to provide samples and data without delay."
-What are your thoughts on your determination to make solid electrolytes a global standard, and on the technology?-
N.NAKAYA"I think it will take time to standardize solid electrolytes and have them take root throughout society. As liquid-based lithium-ion batteries continue to evolve, I would like to see them take a certain position, but it may take some time for them to take over the world. In that sense, this is not something that will end with our generation. As engineers, we want to make sure to leave behind everything that needs to be left behind, including patents, experimental data, and records.
What we are currently facing is bringing all-solid lithium battery to the world. First of all, we want to take full responsibility and complete the project until the time comes for demonstration."
Y.WASHIDA"I feel that there are many people in this department who take pride in each process and research. The younger generation also take pride in their work. They research hard, obtain patents, write many reports, and leave behind results that will lead to the future. When I go to the site with young staff engineers to test run the product, they say, 'I'll see this through,' and sometimes even stay behind to help. I think it's important to nurture people who have that kind of determination and drive."
-"solid electrolytes" are positioned as one of Idemitsu's four key businesses. What kind of future do you want to create with "solid electrolytes"? -
N.NAKAYA "It's not just about selling our materials. We want to realize the rapid charging and improved driving range expected of all-solid lithium battery and make a difference to people around the world.
It's said that the number of Japanese Nobel Prize winners has been decreasing recently, and frankly, as a Japanese person, I feel frustrated by this. Idemitsu wants to continue to play a central role in Japanese industry, and I want to promote Japan's technological capabilities."
Y.WASHIDA"I believe that solid electrolytes hold a lot of hidden potential. Right now we're mainly focusing on EVs, but all-solid lithium battery may be used in other applications, not just drones but even flying cars. As people's lives become richer and more convenient, we can take on even more challenges. I hope that they will become the material for such challenges. I believe a bright future awaits."
-What do you think is essential to making this future a reality?-
N.NAKAYA "I believe that failure leads to success. In the world of research, we often say that there are 'one thousand and three' (out of 1,000 ideas, only three will succeed), so I want to make many failures and lead to many successes. The biggest risk is to fail and get discouraged, to stop moving forward. This is a business and technology that has been passed down for 30 years, so we want to continue to persevere and take on new challenges in order to pass the baton to the next generation."
Y.WASHIDA "I think I've been blessed with great bosses. There was a time when I was given strict guidance on my work, but now I only have fond memories and am grateful. Excellent people work with the conviction that 'I will do whatever it takes and absolutely produce results.' I want to inherit that mindset, while also protecting the things that I will not compromise on, and demonstrate that through my actions and results. I want to nurture and increase the number of people with that mindset."
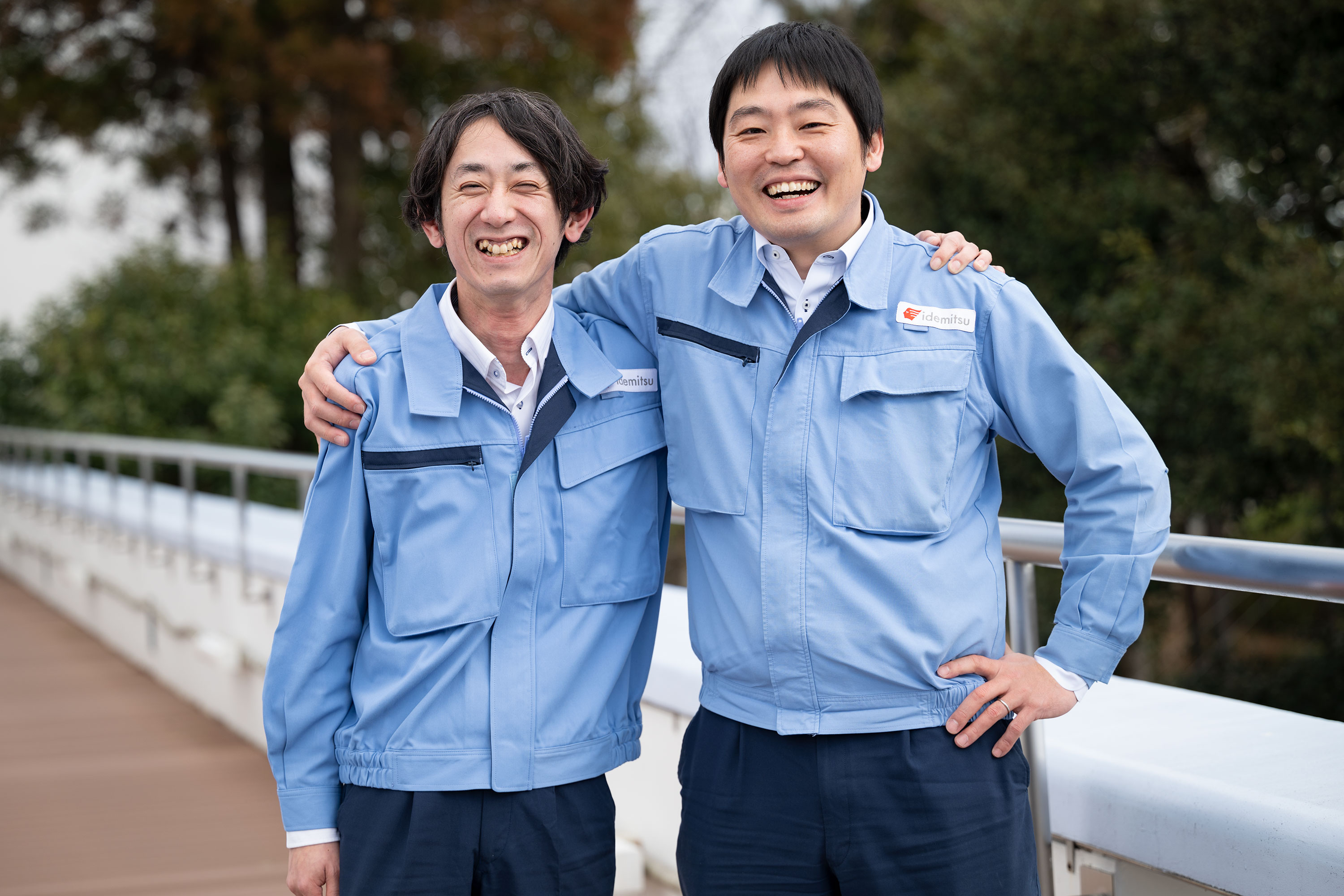
A future that was once thought of as a pipe dream is becoming a reality thanks to Idemitsu's technological capabilities and teamwork. We spoke to the two leaders of the development and mass production teams about each other.
N.NAKAYA:
"A key person in mass production and a reliable partner"
Mr. Washida is a person with the ability to get things done once he has decided to do something. Even if I ask for advice, he doesn't reject it right away, but instead accepts it and says "I understand," and then starts a discussion. Even if something seems impossible, he is always willing to discuss it and say, "If we do it like this, it can be done," and I can rely on him.
Y.WASHIDA:
"A great researcher and a kind manager"
We have a good distance between us. Nakatani-san gathers more information, so I try to be proactive in picking it up. Even though our job duties are different, we have the same goal, so we try to talk about anything openly, and Nakatani-san is someone who can do that. However, I recently realized that when he calls me by name with a smile on his face, it's usually a problem that he's asking for (laughs).
*As of February 2025
Related interviews
-
「人が中心の経営」
創業の精神を
守りながら、
未来を創り上げる。2025.01.30 UPHuman resources departmentT. SUGIUCHIR.IWAOY. NISHIYAMA -
SAFの
供給体制を構築し
脱炭素社会の
実現につなげる。2024.08.02 UPCarbon Neutral Transformation Department
Biomass and Synthetic Fuel Business Promotion SectionK.TOYOTSU -
有機ELの世界に
活路を見出した
先達の意思を継いで
未来を切り拓く。2024.04.30 UPAdvanced Materials Company Electronic Materials DepartmentM. FUNAHASHI