Leading a carbon neutral/circular society
3 business domains
"I think the oil industry and Idemitsu will face tough times."
Some people may have such an image.
We have the absolute knowledge, technology, and infrastructure that we have cultivated as a top runner in our mainstay Petroleum business.
We believe that the 3 business domains are not to be started anew on a zero-based basis, but rather to "evolve" by leveraging those "assets".
Yes, we are actually one step ahead.
In the laboratory, it may be possible to easily create new energies and materials.
However, we have a mission to provide a stable supply of energy and "protect people's lives."
We need to continue supplying energy in large quantities, not in small quantities, and in a stable manner.
If Idemitsu doesn't do it, who will? Idemitsu has to do it.
We will make a carbon-neutral, recycling-oriented society a reality in 2050 with our own hands.
“Power of people” and “inherited infrastructure” that lead to realization
The future that can be changed because of Idemitsu
Human resources, infrastructure, technology, knowledge
For many years, Idemitsu has been involved in oil refining, petrochemical manufacturing, and the development of a variety of materials. The equipment we have built has been passed down with care, and in the process of business, people have been trained and a variety of knowledge has been accumulated.
3 business domains will strategically leverage and evolve these assets.
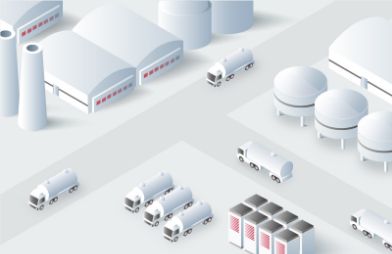
CNX * Center
An example of strategically combining Idemitsu's assets is establishment of CNX Center concept. The concept is to transform our group refineries and complexes, which
are our petroleum and petrochemical manufacturing bases, into a next-generation energy
supply base without the large-scale construction of new facilities.
Unlike oil, which is in demand throughout the country, needs for next-generation energy and carbon-neutral solutions are expected to differ depending on the region. We assess the characteristics and needs of hydrogen, ammonia, chemical recycling, and other options, and proceed with initiatives at Refineries and Complexes more suitable for realizing these needs.
*Abbreviation for Carbon Neutral Transformation.
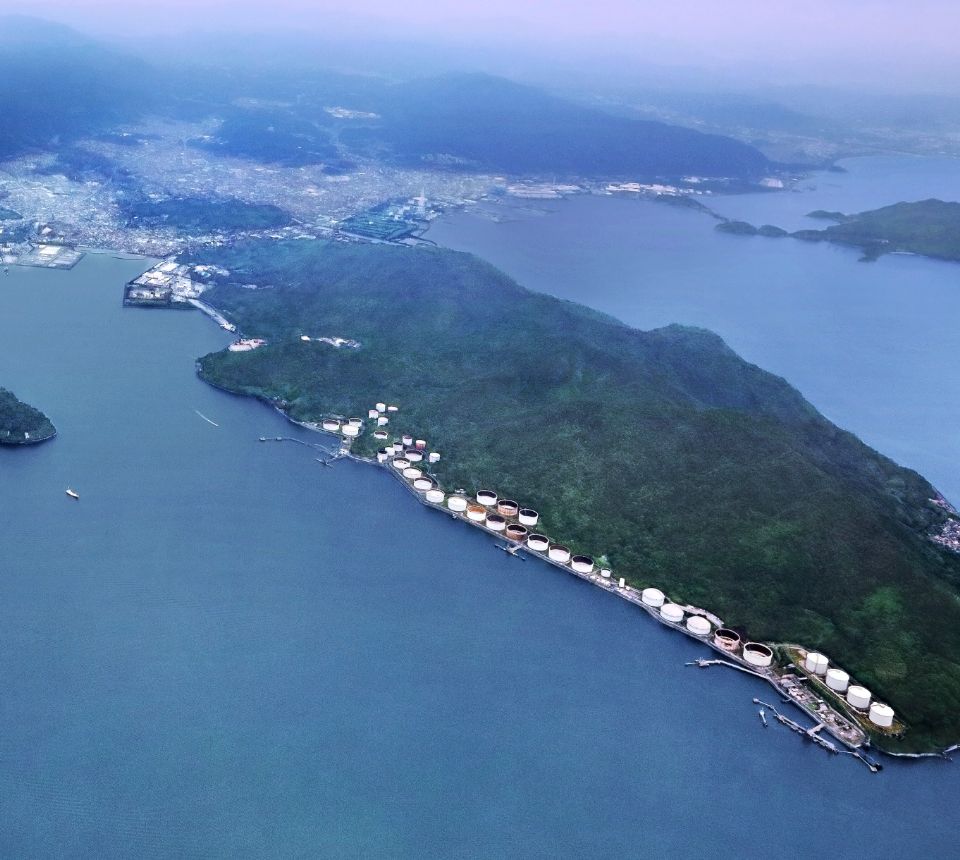
Energy one step ahead
Ammonia
Ammonia does not emit CO₂ when burned, so it is attracting attention as a potential alternative energy source to coal and heavy oil. Idemitsu has long handled ammonia in the oil refining process. Utilizing this knowledge, the company aims to set up an ammonia import base using existing infrastructure at Tokuyama Complex (Shunan City, Yamaguchi Prefecture) and supply ammonia to each company in the petrochemical complex.
We are accelerating our consideration of building a clean ammonia supply chain, including by working with Mitsubishi Corporation to procure ammonia from manufacturing projects in North America and to improve the efficiency of ammonia carriers and import receiving centers. In Australia, we are also leveraging the business foundation we have cultivated in the coal business to participate in studies and surveys regarding ammonia production and export, steadily accumulating knowledge about supply chains, including procurement.
We are also working on developing technology that does not reduce thermal efficiency when ammonia is mixed with petroleum or heavy oil, and on research and development to significantly reduce CO₂ emissions during ammonia production. The Haber-Bosch process, which is currently widely used as a method of producing ammonia, requires a large amount of energy to produce ammonia by reacting hydrogen and nitrogen under high temperature and pressure, which is problematic because it produces a large amount of CO₂ and is costly. To solve this problem, we are working with the University of Tokyo and others to establish and mass-produce ammonia production technology under mild reaction conditions at room temperature and pressure, with the aim of realizing a carbon-free ammonia production process.
- June 2021
- Started of joint study on building an ammonia supply chain using existing facilities at Tokuyama Complex with IHI
- January 2022
- "Development of ammonia production technology at ambient temperature and pressure" adopted by NEDO Green Innovation Fund
- August 2022
- The “Basic Study on the Establishment of Ammonia Supply Center at the Shunan Industrial Complex” was adopted for a subsidy program for “measures to promote the introduction of non-fossil energy (Support Project for Establishment of Hydrogen and Fuel Ammonia Supply Center at Industrial Complex)” by the Agency for Natural Resources and Energy, Ministry of Economy, Trade and Industry (METI).
- November 2022
- Started of research for production and export of green ammonia at Abbott Point Port in Australia
- April 2023
- Agreement reached with Korea Electric Power Corporation to consider collaboration regarding ammonia procurement, marine transportation, and supply
- July 2024
- World's highest performance achieved in continuous electrolytic synthesis of ammonia at room temperature and pressure
- October 2024
- Agreement reached to consider participation together with Mitsubishi Corporation in ExxonMobil's clean hydrogen ammonia production project in Baytown, U.S.
Schedule for realization
-
As of July 1, 2025
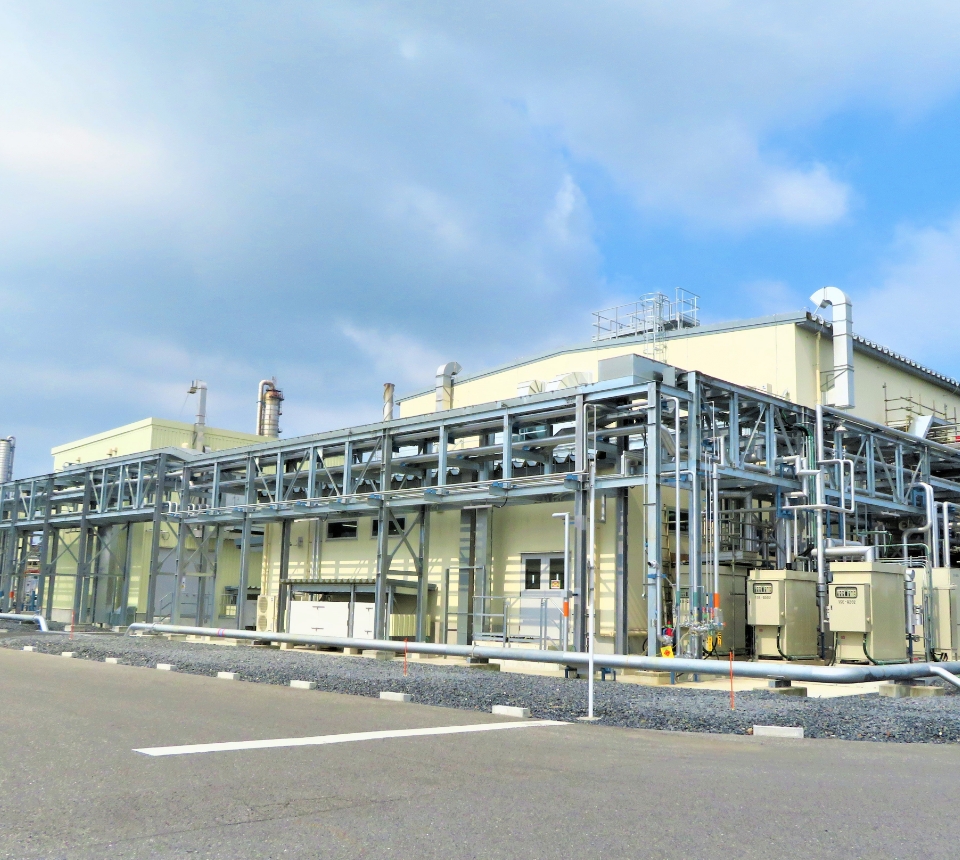
Diverse resource conservation / circulation solutions
Next Generation Battery Materials
all-solid lithium battery are attracting attention as a promising next-generation lithium-ion battery. For electric vehicles (EVs), they are expected to extend driving range, shorten charging times, and improve safety, and are said to hold the key to the spread of EVs. We are working on the development of materials and mass production technology for "solid electrolytes" which are the materials used in "all-solid lithium battery." "Lithium sulfide," an intermediate raw material for solid electrolytes, is a by-product of the petroleum refining process, and we have been researching useful ways to utilize it for many years.
- 1994
- Established lithium sulfide manufacturing technology
- 2001
- Started research into solid electrolytes
- 2004
- Achieved the same level of ionic conductivity as electrolytes for the first time in the world as a sulfide-based solid electrolytes
- November 2021
- Small pilot facilities plant 1 begins operation
- April 2022
- "Development of mass production technology for sulfide-based solid electrolytes" adopted by NEDO Green Innovation Fund
- June 2022
- Started Joint development with Umicore S.A. of high-performance materials for all-solid-state batteries
- June 2023
- Decided to increase capacity of small pilot facilities plant 1, and announced start of operation of plant 2
- October 2023
- Started cooperation toward mass production of all-solid-state batteries for BEVs.
- October 2024
- Announcement of the basic design of a large-scale pilot device for practical use of solid electrolytes
Schedule for realization
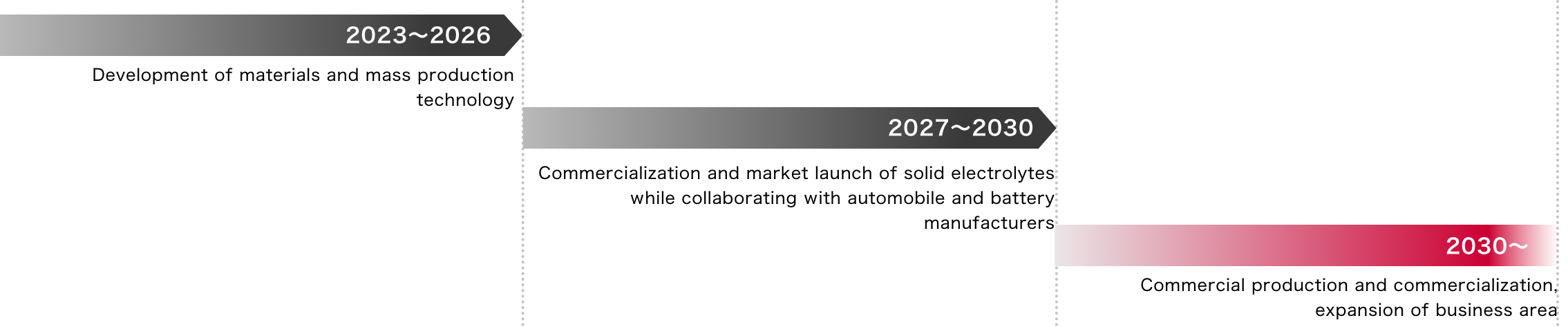
-
As of November 13, 2024
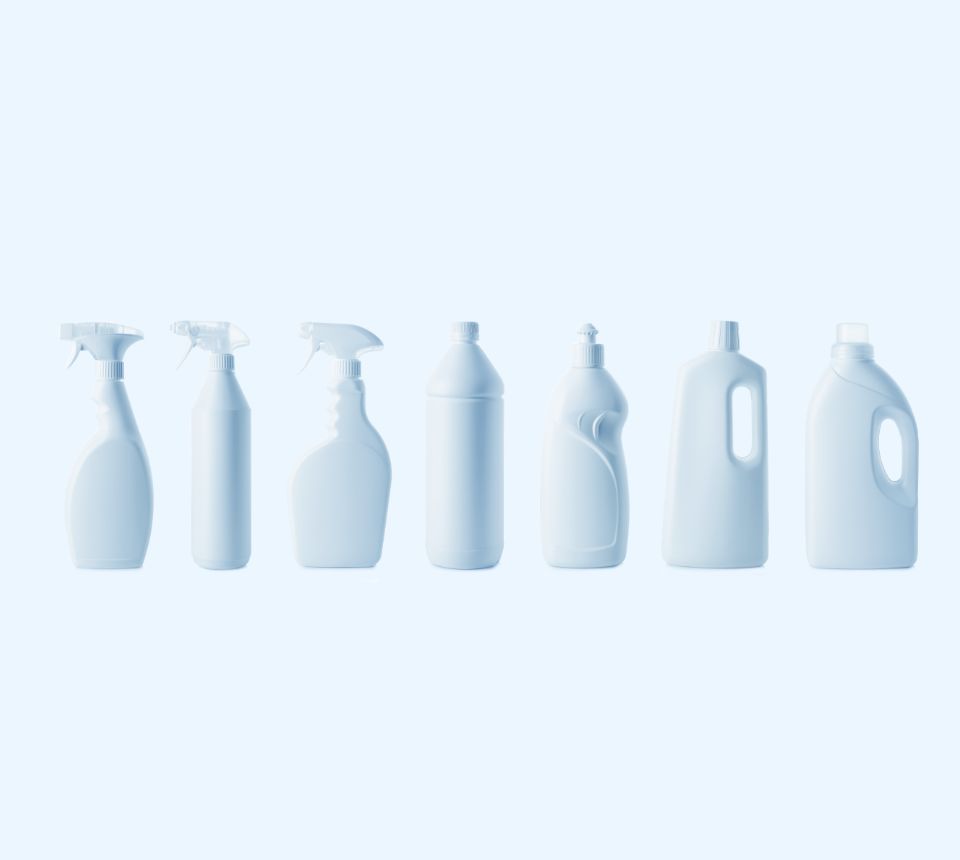
Diverse resource conservation / circulation solutions
Recycling of Used Plastics
Although there is growing interest in the problem of marine plastic litter and climate change, only 20% of used plastic resources in Japan are recycled. In order to break through this current situation, Idemitsu Kosan is working on "oil conversion technology, "which breaks down used plastic to a state similar to crude oil, and is one of the method called "chemical recycling. "We are working on developing technology that can convert plastics into oil even when multiple plastics are mixed together, which has been considered a bottleneck in recycling. The "Produced oil" produced through oilification is recycled as a raw material for petrochemical products and fuel oil by utilizing existing oil refining facilities and petrochemical equipment.
- 2019
- Started development of "oil conversion technology" for used plastics with Environment Energy Co., Ltd.
- 2021
- "Oil conversion technology" demonstration study begins
- September 2022
- Agreed to perform basic design of converting equipment for recycling of
used plastics into Oil in the Chiba Complex area
Started to consider a business alliance with Terrarem Group and Maeda Industrial regarding the procurement of used plastics - April 2023
- Established "Chemical Recycle Japan Co., Ltd." as a joint venture with Environment Energy
- From 2023
- Started demonstration experiments with various industry partners to recycle used plastics Learn more
Schedule for realization
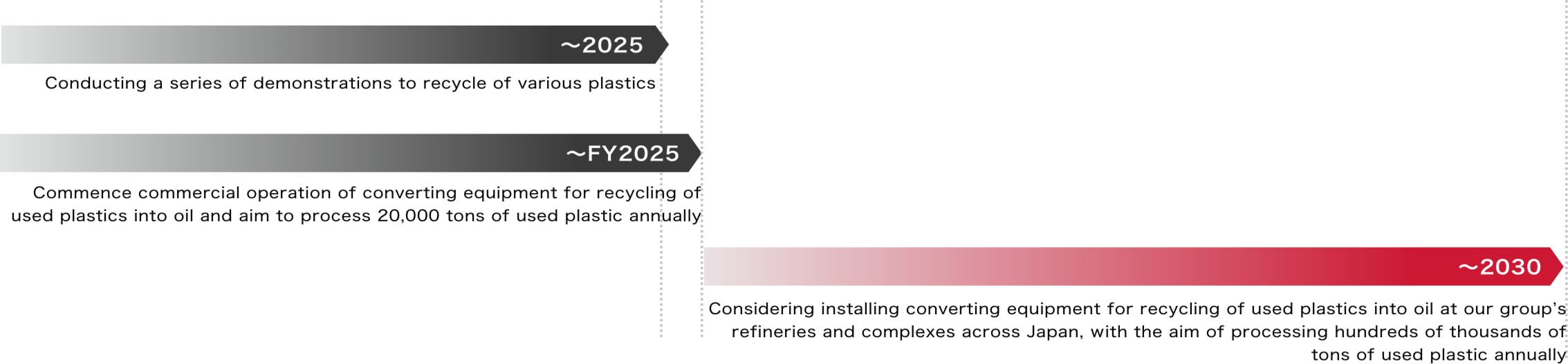

Smart Yorozuya
Various types of SS
- Evolving into a "lifestyle support hub" -
The "Smart Yorozuya'' concept is not bound by the fixed concept of service station = refueling, but instead evolves into a support base for daily life that solves local issues. Based on this concept, six representative types have been created, including "environmentally friendly eco stations" and "EV charging/maintenance stations" that utilize domestic wood and serve as circular bases, such as by installing solar panels. I am presenting it. Furthermore, we are accelerating our digital strategy to provide even more convenient use. Through the official app "Drive On,'' you can now do everything from service reservations to payments in one stop. Since the challenges of daily life change depending on the region and the times, we will continue to evolve into Yorozu (infinitely and diversely) by accurately capturing needs. We will continue to be a hub of energy and mobility while being close to people's lives.
- May 2021
- Smart Yorozuya concept announced
- September 2021
- Official app “Drive On” released
- November 2022
- Payment function “Mobile Drive Pay” installed in official app Drive On
- November 2022
- Opening of the first environmentally friendly eco station “TypeGreen”
- September 2023
- Opening of the first "apolloONE" store specializing in mobility services
- December 2023
- service station will be unified under the "apollostation" brand
Schedule for realization
